Dokuma (98)
Tekstilde farklı yöntemler vasıtası ile kumaş üretimi mümkün kılınabilmektedir.
- Dokuma
- Örme
- Dokusuz yüzey oluşturma yöntemleri
İle geleneksel, iki boyutlu kumaşların üretimi sağlanabilmektedir.
Anizotropik yapıya sahip olan iki boyutlu kumaşlar, yüzey alanı ile kıyaslandığında oldukça düşük bir kalınlık değerine sahiptirler, dolayısıyla kalınlıkları yönünde düşük mekanik performans göstermektedirler.
Tekstil lifleri ve kumaşlar kompozit malzeme üretiminde yaygın olarak kullanılmaktadır. Tekstil kompozit malzemeler savunma, medikal, havacılık endüstrisi gibi birçok endüstri dalında uygulama alanı bulmaktadır.
Tekstil kompozit malzemeler, düşük ağırlıklarına nazaran sahip oldukları yüksek mukavemet değerleri ile metal ve seramik malzemelerden yüksek mekanik davranış göstermektedirler.
- İki boyutlu kumaşlar ile üretilen kompozit malzemeler, düşük kalınlık değerine sahip oldukları için kalınlıkları doğrultularında düşük mekanik davranış sergilemektedirler.
- İki boyutlu tekstil kompozit malzemelerinde katlar arası ayrılma olarak ifade edilen delaminasyon problemi meydana gelmektedir.
- İki boyutlu kompozit malzemelerde gözlenen problemler, üç boyutlu kumaşların üretilmesi için önemli bir neden teşkil etmiştir.
- Üç boyutlu kumaşlar dokuma, örme, dokusuz yüzey oluşturma ve diyagonal örme yöntemleri gibi tekstil üretim yöntemleri ile elde edilebilmektedir.
- Üç boyutlu kumaşlar kompozit malzemelerde meydana gelen delaminasyon problemini tamamen ortadan kaldırmaktadır.
Bunun yanı sıra elde edilmek istenen son ürünün şekline yakın üretimi mümkün kılmaktadır. Böylece üretim maliyetleri ve malzeme telef miktarlarında ciddi bir azalma sağlanmaktadır.
Üç Boyutlu Kumaşların Üretim Yöntemleri
Üç boyutlu kumaşlar dokuma, örme, diyagonal örme, dokusuz yüzey oluşturma ve dikme gibi tekstil üretim yöntemleri ile elde edilebilmektedir.
Üç Boyutlu Örme Yöntemi
Üç boyutlu örme kumaşların üretimi geleneksel, iki boyutlu örme kumaşların üretiminde olduğu gibi atkılı ve çözgülü örme yöntemleri ile elde edilebilmektedir.
Atkılı örme yöntemi ile istenen son ürüne oldukça yakın şekle sahip, üç boyutlu örme kumaşların üretimi sağlanabilmektedir.
Üç boyutlu örme kumaşların atkılı örme makinelerinde üretimi;
Makinelere modifiye ile yataklar ve elektronik donanımlar ile sağlanabilmektedir.
Üç boyutlu atkılı örme kumaşların bir diğer önemli avantajları ise istendiği takdirde boyuna yönde dolgu ipliklerinin yapı içerisine dâhil edilebilmesidir.
Atkılı örme yöntemi ile elde edilen bu kumaş türlerinde yaşanan en önemli problem;
Yapının fazla hacimli ve boşluklu olmasıdır. Birim hacim başına düşen boşluk sayısının fazla olması yapının lif/ hacim oranının düşmesine sebebiyet vermektedir. Bu durum yapının düşük bir mukavemet değerine sahip olmasına neden olmaktadır.
Çözgülü örme makineleri ile elde edilen üç boyutlu örme kumaşlar, atkılı örme makinelerinde üretilen yapılara nazaran son yıllarda yüksek derecede rağbet görmektedir.
Çözgülü örme makineleri ile elde edilen üç boyutlu örme kumaşlar;
İki boyutlu dokuma kumaşlara nazaran yüksek derecede elastisite modülü ve mukavemet değerlerine sahiptir.
Bu farkın sebebi;
- Karbon
- Cam
- Bazalt vs.
Gibi yüksek modüllü liflerin çözgülü örme yapıların içerisinde daha az kıvrıma sahip olarak yer almalarıdır. İplik yapısında kıvrımın azalması mukavemette artışa sebebiyet vermektedir. Ayrıca kompozit malzeme üretiminde iki boyutlu dokuma kumaşların yerine bu yapıların tercih edilmesi; kumaş telef miktarının ve üretim maliyetlerinin ciddi derecede azalmasını sağlamaktadır. Aşağıda çözgülü örme yöntemi ile üretilen üç boyutlu örme kumaş gösterilmektedir.
Üç boyutlu çözgülü örme kumaşlar 1980’ li yılların başında üretilmeye, 1990’ lı yıllarda kompozit endüstrisinde kullanılmaya başlanmıştır.
Bu kumaş türlerinde Üretim maliyetlerinin düşük olması, istenen özellikler doğrultuşunda dizayn edilebilme kabiliyetleri gibi üstün özelliklerinden dolayı;
- Jeotekstiller
- Pnömatik sistemler
- Araba ve uçaklarda bazı parçalarının üretimi
- Çeşitli vücut kısımları ve yapay damarların üretimi
Gibi birçok farklı alanda kullanım imkânı bulabilmektedirler.
Çözgülü örme makinelerinde bu kumaş türlerinin üretimi;
- Lif tabakalarının istenen doğrultuda yatırılıp, çözgülü örme ilmeği vasıtası ile bu tabakaların bağlanmasıyla sağlanmaktadır.
Mayer ve Liba firmaları farklı üretim teknikleri ile bu yapıların üretimini mümkün kılmaktadır. Mayer firmasının geliştirdiği sistemde dört farklı lif tabakasının 0˚, +45˚, -45˚, 90˚ yönlerinde yatırılması ve ilmek vasıtası ile bağlanarak üretilmesi sağlanmaktadır. Liba firmasının geliştirdiği yöntemde ise kumaşa dâhil edilen lif tabaka sayısı yedi’ ye çıkabilmektedir. Aşağıda Liba firmasının üretim tekniği görülmektedir. Liba üretim tekniği ayrıca dokusuz kumaşların sisteme dâhil edilebilmesini mümkün kılmaktadır.
Yapı içerisinde bulunan lif tabakaları;
İstenen doğrultularda yapıya mukavemet kazandırırken
Çözgülü örme ilmeği;
Yapının kalınlık yönünden mukavemetinin artmasını sağlamaktadır.
Üç boyutlu çözgülü örme makinelerinde ilmek:
- Zincir
- Trikot
Olmak üzere iki farklı şekilde elde edilebilmektedir. İlmek, yapının bütünlüğünü sağlarken mukavemette ve zarar toleransında ciddi derecede artış meydana getirmektedir. Zarar toleransı, malzemenin yapısal bir özelliğidir. Malzemenin, yapısında meydana gelen hasarın, tamir işlemi gerçekleşene kadar malzeme güvenilirliğini belirli sınırlar içerisinde tutabilme kabiliyeti olarak ifade edilebilir.
Üç Boyutlu Dokusuz Yüzey Oluşturma Yöntemi
Üç boyutlu dokusuz yüzeylerde, yapıyı oluşturan iplikler arasında herhangi bir bağlantı bulunmamaktadır. Bu yapılar iğneleme ve dikişle birleştirme yöntemleri ile üretilebilmektedir.
İğneleme yönteminde iplikler; istenen doğrultularda sisteme yatırılmaktadır fakat bu iplikler arasında herhangi bir bağlantı bulunmamaktadır. Sonrasında iğneler vasıtası ile ipliklerde yer alan elyafın birbiri içerisinden geçerek birleşmeleri ve bir yüzey oluşturmaları sağlanmaktadır. Aşağıda iğneleme yöntemi ile oluşturulan bir yüzey ve üretim yöntemi görsel olarak ifade edilmektedir.
Dikiş ile yüzey oluşturma yönteminde liflerin ya da ipliklerin oluşturduğu tabakaların dikiş işlemi ile birleştirilmesi sağlanmaktadır. Yapılan bu işlemde dikiş türü, dikiş ipliği çeşidi ve numarası, birim alandaki dikiş yoğunluğu büyük önem arz etmektedir.
Üç boyutlu dokusuz yüzeylerde dikiş ipliği yoğunluğu 0,4 – 25 dikiş/ cm² arasındadır. Genellikle dikiş ipliği olarak kevlar tercih edilmektedir. Çünkü kevlar diğer liflere nazaran yüksek mukavemet ve esneklik değerlerine sahiptir.
Dikiş işlemi ile dokusuz yüzeylerin elde edildiği makinelerde dikim kafası bir veya birden fazla olabilmektedir. Makinede bulunan dikim kafa sayısının sınırlı olması, belirli bir yüzey kalınlık değerine kadar dikim işleminin yapılabilmesi, yüzeyin sınırlı bir en değerinde elde edilebilmesi bu makineler için başlıca sorunları teşkil etmektedir.
Günümüzde sanayi tipi makineler azami 1 m en ve 5 mm yüzey kalınlığı değerlerinde çalışabilmektedir. NASA’ nın bu yapıları elde etmek için kullandığı makine 28 m uzunluğunda olup, 15 m’ de dikim yapabilmekte, 3 m ende ve 40 mm kalınlıktaki yüzeylere dikme işlemi uygulayabilmektedir.
Üç boyutlu dokusuz yüzeylerin üretimi iki boyutlu dokuma kumaşlara nazaran daha kolay ve ucuzdur. Aynı zamanda bu yapılar ile elde edilen kompozit malzemelerin yorulma ve darbe dayanımı geleneksel dokuma kumaşlara nazaran daha yüksektir.
Kompleks şekillerde yer alan, kavisli bölgelerin günümüz sanayi makineleri ile dikiminin zor olması bu yapıların önemli bir problemini oluşturmaktadır.
Dikiş yoğunluğu, iplik türü ve numarası gibi konularda da yeterince çalışma yapılmamıştır. Bu konuların aydınlatılmamış olması kullanımlarının artmamasının bir diğer önemli sebebini oluşturmaktadır. Bu konuda ARGE çalışmalarının yapılması gerekmektedir. Ancak bu ARGE çalışmalarına diğer alanlarda olduğu gibi iki tarafın da haklarını koruyan sağlam bir sözleşme yapılması kaçınılmaz bir gerçektir.
Üç Boyutlu Diyagonal Örme (Braiding) Yöntemi
Üç boyutlu diyagonal örme yöntemi, üç boyutlu kumaş üretimi için tarihte kullanılan ilk yöntemdir.
1960’ li yılların sonlarında;
- Roket motorunda, metal alaşımlarına nazaran %30- 50 arasında ağırlığın azaltılması amacı ile üretilmiştir.
Diyagonal örme yöntemi ile elde edilen üç boyutlu kumaşlar;
- Medikal
- Uzay
- Ulaşım
Gibi birçok farklı alanda kullanım alanı bulabilmektedir.
Diyagonal örme yöntemi ile son şekle oldukça yakın yapıların üretimi mümkün kılınmaktadır. Bu durum üretim maliyetlerini ve atık iplik, kumaş miktarını ciddi derecede azaltmaktadır. Aşağıda diyagonal örme yöntemi ile üretilmiş üç boyutlu kompozit malzemeler görülmektedir.
Diyagonal örme yöntemi ile elde edilen üç boyutlu yapılarda eksenel ve örücü iplikler olmak üzere iki farklı iplik grubu bulunmaktadır;
- Eksenel iplikler; mukavemet istenen doğrultuda yapı içerisine dâhil edilirken, iplik bağlantıları örücü iplikler ile sağlanmaktadır. Örücü iplikler mekiklerden sisteme beslenmektedir.
- Örme sistemi örücü iplik bobinlerinin yer değişim hareketi ile sağlanmaktadır.
Aşağıda diyagonal örme kumaş, örücü iplik bobinleri ve bobin mekanizmaları görülmektedir.
- Üç boyutlu diyagonal örme kumaşlar köşeli ya da dairesel olarak üretilebilmektedir.
- Bu yapıların üretimi amaca bağlı olarak dairesel ya da köşeli makinelerde yapılmaktadır.
- Üç Boyutlu diyagonal örme kumaşlar adım sayılarına göre sınıflandırılmaktadır.
Makinenin bir devrinde meydana gelen örme işlemi; adımı ifade etmektedir. Üç boyutlu diyagonal örme kumaşlar iki, dört ya da çok adımlı olabilmektedir. İki adımlı diyagonal örme yöntemi 1987 yılında Popper ve McConnell tarafından geliştirilmiştir.
Aşağıda iki ve dört adımlı diyagonal örme kumaşların birim örgü desenleri gösterilmektedir.
Küçük boyutlu yapıların üç boyutlu diyagonal kumaşlar ile üretimi oldukça ucuz ve kolay bir işlemdir. 100 mm’ nin üzerinde ene sahip kumaşların diyagonal örme yöntemi ile üretilmesinde çeşitli problemler ortaya çıkmaktadır. Çünkü üretilmek istenen ürünün boyutunun artması, makinenin de boyutunun arttırılması gerekliliğini ortaya çıkarmaktadır.
Bu yapıların uçak üretiminde yaygın bir biçimde kullanılamamalarının en önemli nedeni;
- Yapıyı üretebilecek olan makinenin boyutundan kaynaklı olarak maliyetin oldukça yüksek ve işlemin zor olmasından doğmaktadır.
Üç boyutlu diyagonal örme kumaşlarla oluşturulan kompozit malzemelerde elastisite modülü;
- Örücü ipliklerin oluşturduğu diyagonal açı, iplik numaraları ve örgü deseni gibi değişkenlere bağlı olarak değişmektedir.
Üç boyutlu diyagonal örme kumaşlar ile oluşturulan kompozit malzemelerin mukavemet değerlerinin iki boyutlu kompozit malzemelere nazaran düşük olması ve büyük boyutlu kumaşların üretiminde makinenin uzun sürede üretime hazır hale getirilmesi ve yavaş olarak çalışması yapının diğer eksilerini oluşturmaktadır.
Günümüzde üç boyutlu diyagonal örme kumaşların otomotiv sektöründe; şase ve şaft imalinde kullanılması üzerine çalışılmaktadır. Eğer hedeflenen başarıya ulaşılabilirse arabalarda %50’ ye varan oranlarda ağırlık kaybı sağlanabilecektir.
Üç Boyutlu Dokuma Yöntemi
Üç boyutlu dokuma yöntemi, üç boyutlu kumaşların üretimi için kullanılan önemli metotlardan birini temsil etmektedir. Üç boyutlu kumaşlar, kompozit malzeme imalinde kullanıldıkları için mukavemet değerleri önem taşımaktadır.
Üç boyutlu kumaş üretim yöntemleri içerisinde dokuma metodu;
Diğer yöntemlere nazaran yüksek mukavemet değerine sahip kumaşların üretilmesini sağlamaktadır. Bu sebepten dolayı diğer üretim yöntemlerine nazaran daha yaygın ve bilinen bir yöntemdir.
Birçok farklı alanda kullanım alanı bulabilen geleneksel dokuma kumaşlar, kompozit endüstrisinde de iki boyutlu kompozit malzemelerin üretiminde tercih edilmektedir. Tekstil kompozit malzemeler havacılık ve savunma sanayisinde; metal ve seramik gibi benzeri malzemelere nazaran düşük ağırlık, yüksek mukavemet değeri birçok üstün özellik sunmaktadır.
İki boyutlu dokuma kumaşlardan üretilen kompozit malzemelerin düşük kalınlık değerine sahip olmalarından dolayı kalınlıkları yönünde ki mekanik performanslarının düşük olması, bu yapıların önemli bir eksiğini teşkil etmektedir.
Diğer yandan tabakalar arasında meydana gelen ve delaminasyon olarak adlandırılan ayrılma problemi, bu yapıların bir diğer problemini oluşturmaktadır.
İki boyutlu dokuma kumaş yapısında bulunan iplikler, dokuma konstrüksiyonun’ dan dolayı fazla miktarda eğilmeye maruz kalmaktadır.
- Karbon
- Cam
- Bazalt
- Vs. gibi
Yüksek modüllü liflerin bu yapılar içerisinde kullanılması; elde edilen kumaşın düşük elastisite modülüne sahip olmasına sebebiyet vermektedir.
Geleneksel dokuma kumaşlar birbirine dik, iki ayrı iplik grubundan meydana gelmektedirler.
Bu kumaşlara çapraz yönde kuvvet uygulanması;
- Atkı ya da çözgü ipliği olarak adlandırdığımız iplik gruplarının yapı içerisinde kaymasına kumaş mukavemetinin
- Çapraz yönlerde düşmesine
Neden olmaktadır.
İki boyutlu dokuma kumaşlarda yaşanan bu problem Triaxial olarak adlandırılan kumaş türlerinin üretilmesine sebebiyet vermiştir.
Triaxial kumaşlarda üç çeşit iplik grubu yer almaktadır. Bu iplikler;
- Yapının mukavemetini çapraz yönde uygulanan kuvvetlere karşı arttırmak için birbirleri ile 60˚ açı yaparak kesişmektedirler.
- İki boyutlu dokuma kumaşlarda yaşanan problemler üç boyutlu dokuma kumaşların üretimi için önemli bir sebep oluşturmuştur.
- Üç boyutlu dokuma kumaşlar, iplik veya kumaş tabakaları tarafından oluşturulan kalınlıkları yönünde; belirli bir boyuta sahip olan yapılardır.
- Üç boyutlu dokuma kumaşlar kalınlıkları yönünde yüksek mekanik karakteristik göstermektedir.
- Entegre bir yapı halde kalınlık değerine sahip olmaları iki boyutlu kompozit malzemelerde gözlenen delaminasyon problemini tamamen ortadan kaldırmaktadır.
- Üç boyutlu dokuma kumaş üretim yöntemleri, yüksek modüllü liflerin x, y ve z yönlerinde düşük kıvrım oranı ile yapıya dâhil edilebilmelerini mümkün kılmaktadır.
- Liflerde kıvrım oranının düşmesi; yapının lif/hacim oranının artmasını sağlamaktadır dolayısıyla kumaşlarda elastisite modülü yükselmekte, mukavemet artışı gözlemlenmektedir.
- Üç boyutlu dokuma kumaş üretim yöntemleri ile karbon, cam, bazalt vs. gibi yüksek modüllü liflerden; 1 inç’ ten 72 inç’ e kadar kalınlık değerine sahip kumaşların üretimi mümkün kılınabilmektedir.
- Üç boyutlu dokuma kumaşların kompozit malzeme üretiminde sahip oldukları bir diğer artı nokta ise komplike şekillerin üretimini sağlayabilmeleri ve net şekle yakın olarak üretilebilmeleridir.
Kompozit malzemeler üzerinde yapılan delme, kesme gibi işlemler malzemelerde yüksek derecede mukavemet kaybına sebebiyet vermektedir. Son şekle yakın üretim; malzemede mukavemet kaybını önlerken malzeme telef miktarı ve işçilik ücretinin azalmasını sağlamaktadır. Yapı içerisinde, kalınlık doğrultusunda yer alan iplikler; kapilar kanal görevi görmektedir. Bu iplikler, kompozit malzeme üretimi için kullanılan reçinenin yapı içerisinde hızlı ve homojen olarak dağılması sağlanmaktadır.
Üç Boyutlu Dokuma Kumaşların Üretim Yöntemleri
Dokuma makinelerinin bir devrinde; açılan bir adet ağızlıktan atkı ipliğinin geçirilmesi ile iki boyutlu dokuma kumaşların üretimi sağlanmaktadır.
Makine hızının çeşitli atkı atma yöntemleri ile oldukça yüksek hızlara çıkabildiği bu yöntemde kumaş kalınlık değeri oldukça sınırlıdır. Ayrıca yapı içerisinde ipliklerin kıvrımlı olarak yer alması bu kumaşların elastisite değerlerinin düşük olmasına sebebiyet vermektedir.
Üç boyutlu dokuma kumaşlarda kalınlık yönünde birden fazla atkı ipliği yer almaktadır. Bu durum kumaşın kalınlık değerine sahip olarak üretilebilmesini sağlamaktadır.
Üç boyutlu dokuma kumaşlarda tefeleme işleminden önce
- Birden fazla ağızlığın açılması gerekliliği Makine hızının düşük bir değere sahip olmasına sebebiyet vermektedir.
- Üç boyutlu dokuma kumaşların üretimi; geleneksel dokuma makinelerinin modifikasyonu ile ya da üç boyutlu dokuma kumaş üretmek amacı ile özel olarak modifiye edilmiş makineler vasıtasıyla sağlanmaktadır.
- Çok katlı yapıların üretimi; bağlayıcı çözgü ipliklerinin sadece dikey yöndeki hareketi ile sağlanabilirken,
- Özel olarak modifiye edilmiş dokuma makinelerinde çözgü ipliklerinin yatay ve dikey yönde hareket ettirilmesi ile üç boyutlu dokuma kumaşların üretimi sağlanmaktadır.
Geleneksel Dokuma Makinelerinin Modifikasyonu ile Üç Boyutlu Dokuma Kumaş Üretimi
Çok katlı dokuma kumaşların iki farklı çözgü grubu kullanılarak üretimi 1974 yılında Greenwood tarafından geliştirilmiştir.
Üç farklı iplik grubu kullanılarak üç boyutlu dokuma kumaşların üretimi sağlanmaktadır. Çözgü iplikleri iki farklı iplik grubundan oluşmaktadır. Bir grup sadece kumaş doğrultusu yönünde uzanırken bağlayıcı çözgü iplikleri kumaşı bütün halde, bir arada tutmaktadır.
Khokar, bu yapıları Noobed olarak adlandırmıştır. Sistem içerisinde yer alan üç ayrı iplik grubu birbiri ile fazla miktarda bağlantı yapmamaktadır. Bu üretim yöntemi ile 17 kat’ a kadar kumaş üretimi sağlanabilmektedir. Aşağıda bu sistemler ile üretilmiş üç boyutlu dokuma kumaş görülmektedir.
Geleneksel dokuma makinelerinin modifikasyonu ile oluşturulan bir diğer üç boyutlu kumaş dokuma sistemi 1990 yılında Mohamed tarafından geliştirilmiştir. Bu sistemde T, I, π vs. profillerine sahip, üç boyutlu dokuma kumaşların üretimi sağlanabilmektedir.
Sistemde, üretilmek istenen profil şekline göre iplik bobinlerinin cağlığa dizimi sağlanmaktadır. Bir grup çözgü ipliği kumaş doğrultusu boyunca; kumaş içerisinde uzanırken diğer çözgü ipliği grubu çerçeveler vasıtası ile aşağı, yukarı yönde hareket ettirilmektedir.
Atkı iğneleri vasıtası ile birden fazla atkı ipliğinin tek bir makine devrinde yapıya dâhil edilebilmesi sağlanmaktadır.
Atkı iplikleri; makine kenarında bulunan örücü iğneler vasıtası ile yapıya bağlanmakta ve tefeleme işlemi ile kumaş oluşumu sağlanmaktadır.
Bu sistem vasıtası ile oldukça yüksek kalınlık değerlerine sahip ve mukavim; profilli üç boyutlu dokuma kumaşların üretimi mümkün kılınabilmektedir. ABD’ de bulunan North Carolina State Üniversitesinde geliştirilen bu makinede mekanizmaların hareketi; elektriklenmeyi önlemek maksadı ile pnömatik sistemler vasıtası ile sağlanmıştır. Ayrıca ipliklerde sürtünmeyi azaltmak için iplikler borular içerisinde makineye taşınmıştır.
Gerçek Üç Boyutlu Dokuma Makineleri İle Kumaş Üretimi
Geleneksel dokuma makinelerinin modifiye edilmesi ile üretilen üç boyutlu dokuma kumaşlarda, makinenin devrinde bir kumaş tabakasının yapıya dâhil edilmesi sağlanmaktadır.
Üç boyutlu kumaşlar üzerine çalışan bilim adamları; bu sistemleri gerçek bir üç boyutlu dokuma makinesi olarak görmeyip, yapıya katılması istenen tüm tabakaların; makinenin bir devrinde kumaşa dâhil edilmesi gerektiğini ifade etmektedirler.
Gerçek üç boyutlu dokuma makineleri ile üretilen yapılar;
- Tek eksenli
- Çok eksenli veya iplik tabakaları arasında kesişmenin olması veya olmaması
Durumuna göre kategorize edilebilmektedir.
Aşağıda Fukuta tarafından 1974 yılında geliştirilen tek eksenli, üç boyutlu dokuma mekanizması görülmektedir.
Yapı içerisinde üç ayrı iplik grubu yer almaktadır. Kumaş doğrultusunda yer alan y iplikleri hiçbir kıvrım yapmadan kumaş boyunca uzanmaktadır. Makinede x ve z ipliklerinin mekikler vasıtası ile yapıya dâhil edilmesi sağlanmaktadır. Bu sistemde iplikler arasında bağlantı bulunmamaktadır.
Geleneksel dokuma makinelerinin modifikasyonu ile üretilen üç boyutlu dokuma kumaşlarda;
- İplikler birbirlerine 90˚ açı yapacak şekilde bağlanmaktadır.
- Bu makinelerde iplikler kumaşa 45˚ açıya sahip olarak dâhil edilememektedir.
Dolayısı ile kumaşlar;
- Çapraz yönde uygulanan kuvvetlere karşı düşük mukavemet göstermektedir.
- Çok eksenli üç boyutlu dokuma makineleri ile +45˚ ve -45˚ açılarına sahip iplik tabakalarının kumaşa tek bir makine devrinde dâhil edilmesi sağlanabilmiştir.
Aşağıda tek eksenli ve çok eksenli birim kumaşlar görseli görülmektedir.
Anahara tarafından1993 yılında geliştirilen, çok eksenli üç boyutlu dokuma makineleri vasıtası ile beş farklı eksene sahip dokuma kumaşların üretimi sağlanabilmektedir. Aşağıda farklı açı değerlerine sahip iplik tabakaları ve üretilen kumaş görülmektedir.
Üç boyutlu dokuma kumaşlar dairesel olarak da üretilebilmektedir. Bilişik tarafından 2000 yılında geliştirilen sistemde beş ayrı iplik grubu yer almaktadır.
Bu iplikler eksenel, radyal, çevresel ve çapraz (+45˚, -45˚) olarak yapı içerisinde yer almaktadır. Sistemde çevresel ve radyal iplikler eksenel ipliklerin etrafında bir dokuma katmanı oluşturmaktadır.
Aşağıda üç boyutlu dairesel dokuma mekanizması ve üretilen kumaş görülmektedir.
Çok eksenli, üç boyutlu kumaşlarda; yapı içerisinde yer alan her iplik arasında bağlantı bulunmamaktadır. Makinelerin tek bir devirde her iplik tabakasını kumaşa dâhil edebilmeleri bu sistemler için oldukça önemli bir gelişme olmuştur.
Khokar tarafından 1997 yılında geliştirilen üç boyutlu dokuma yönteminde her bir iplik grubunun birbiri ile bağlantı yapması amaçlanmıştır. Bu yöntemde çözgü iplikleri; çeşitli sistemler vasıtası ile yukarı, aşağı ve sağa, sola hareket ettirilerek kumaş üretimi sağlanmıştır.
Üç boyutlu dokuma kumaşlar kompozit endüstrisinde kullanıldıkları için mukavemet ve ağırlık değerleri oldukça büyük bir önem taşımaktadır. Yapı içerisinde bulunan her bir ipliğin bağlantı yaptığı üç boyutlu dokuma kumaşlar; diğer kumaş çeşitlerine nazaran oldukça yüksek mukavemet değerlerine sahiptir.
Üç Boyutlu Dokuma Kumaşların Sınıflandırılması
Üç boyutlu dokuma kumaşlar birçok farklı şekilde kategorize edilebilmektedir. Dokuma prosesi, ipliklerin yapı içerisine yerleşme geometrisi, birim kumaş hücrelerinin mikro ve makro yapısı; bu kumaşların sınıflandırılabildiği konulardır.
Birçok farklı bilim adamı üç boyutlu dokuma kumaşlar üzerine sınıflandırma yapmıştır. Khokar bu yapıları dokuma prosesi, kullanılan iplik grupları ve oluşturulan yapıya bağlı olarak altı grupta sınıflandırmaktadır.
Chen ise birim kumaş hücresinin makro yapısını dikkate alarak dört farklı grup oluşturmuştur.
Bu sınıflandırma yönteminde kumaşlar:
- Solid
- Hollow
- Nodal
- Shell
Olarak ayrılmaktadır.
Üç boyutlu dokuma kumaşları, yapılarında bulunan ipliklerin; yapıya yerleşim geometrilerine göre ayırmak da mümkündür.
Bu kapsamda üç boyutlu dokuma kumaşlar:
- Orthogonal
- Açılı interlok
Olmak üzere iki gruba ayrılmaktadır.
Orthoganal yapılarda bağlayıcı iplikler kumaş katları ile 90˚’ lik açı yapmaktadır.
Açılı interlok kumaşlarda ise çözgü iplikleri ve atkı ipliklerinin oluşturduğu kumaş tabakaları arasında belirli bir açı değeri bulunmaktadır. Bu değer üretilmek istenen yapının özelliklerine bağlı olarak ayarlanabilmektedir. Her iki kumaş çeşidi için yapıya güçlendirici iplikler ilave edilebilmektedir. Bu iplikler kumaş doğrultusunca uzanarak kumaşın lif/ hacim oranının artmasını ve dolayısıyla mukavemetin yükselmesini sağlamaktadır.
- Orthogonal kumaşlar açılı interlok yapılara nazaran yüksek lif/ hacim oranına sahiptirler. Açılı interlok yapılar ise orthogonal kumaşlara nazaran yüksek elastikiyet özelliklerine sahiptirler.
Orthogonal ve açılı interlok kumaşlar; yapılarında bulunan bağlayıcı ipliklerin geometrilerine bağlı olarak iki gruba ayrılabilmektedir.
Eğer bağlayıcı iplik:
- Kumaş içerisinde sadece belirli katlar arasında bağ yapıyor ise kattan kata,
- Kumaş kalınlığı boyunca bağlama işlemini gerçekleştiriyorsa kumaş kalınlığı boyunca orthogonal ya da açılı interlok kumaş olarak adlandırılabilmektedir.
Bilinçlenen ve tüketim alışkanlıkları değişen tüketiciler, bir giysinin dış kumaşına, görüntüsüne ve işçiliğine verdiği önemi ve dikkati, giysinin iç kısmını kaplayan malzemelere de vermektedirler.
Günümüzde konfeksiyon sanayinde önemi sürekli artan astarlık kumaşlar, giysinin tam bir bütünlük oluşturması için diğer yardımcı malzemeler ve aksesuarlar içerisinde ayrı bir öneme sahip olmaktadır.
Astarlık kumaşlar, giysilerin iç tarafının bir kısmını veya tamamını kaplayarak dikişleri örten, üst kumaşın tipine uygun ağırlığa, sağlamlığa, renge, tuşeye ve hareket yeteneğine sahip, kumaşlardır.
Astarlık kumaşlar insan vücuduyla ilk temas eden yüzeylerdir. İnsan vücudunun hareketleriyle birlikte sürtünmeye, gerilmeye vb. etkilere maruz kalır. Giysi kalitesi açısından bu kumaşlarda mukavemet önemlidir. Astarlık kumaşlardan beklenen en önemli özellik; giysinin kullanım sırasında fonksiyonelliğini ve rahatlığını bozmadan, giysi içindeki görünüşü daha net hale getirmektir. Ayrıca, dış kumaş ile aynı performans ve dayanım özelliklerine sahip olması, kullanım sırasında uygulanan temizleme işlemlerinden dolayı boyutsal değişiklik göstermemesi ve dış kumaş ile aynı zamanlarda ömrünü tamamlaması beklenmektedir. Uzun süreli kullanımlarda boncuklanma değerlerinin, aşınma ve kopma mukavemetlerinin, renk ve ter haslıklarının iyi sonuçlar vermesi tüketici tatmini açısından sağlanması gereken temel şartlardan bazılarıdır.
Elde edilecek olan kumaşın özellikleri göz önünde tutularak astarlık kumaş üretiminde genellikle viskon, floş asetat ve triasetat, naylon ve polyester elyafları ile bu elyafların karışımları kullanılır.
Viskon Astarlıklar
Viskon astarlıklar iyi bir su ve ter emme özelliklerine sahiptir. Bunun yanı sıra çabuk kırışma ve fazla çekme gibi dezavantajları vardır. Ayrıca ıslak mukavemetleri düşüktür. Bununla beraber, ipeğe benzer kaygan bir tuşe ve dökümlülük gösterirler.
Modifiye viskon elyaflar olan modal elyafların kullanıldığı astarlıklarda iyi form tutma, yüksek yaş mukavemet ve iyi statik elektriklenmeme özellikleri mevcuttur.
Floş Astarlıklar
Floş ipliği, viskonun kesiksiz filament formunda üretilen şeklidir. Yüksek parlaklık ve statik elektriklenmeme özelliklerine sahiptir. İyi su ve ter çekme özelliklerine rağmen ıslak mukavemeti çok azdır. Bu nedenle yıkamaya karşı hassastır. Floş astarlıklar yüksek dökümlülük ve ağır gramaj özelliklerine sahiptirler. İyi bir ısı yalıtımı sağladığı için özellikle yazlık giysilerde tercih edilmektedir. Bu astarlar çok kaygan olduğu için dikiş yerlerinde doku kayması oluşabilir. Bu sebeple uygun dikiş tipinin seçilmesi çok önemlidir. Fazla çekme gösterdiği için kesimde önce çekme oranları tespit edilerek gerekli pay bırakılmalıdır.
Asetat ve Triasetat Astarlıklar
Asetat lifleri diğer liflere göre daha düşük kopma mukavemetine sahiptirler. Esnek, kaygan, parlak, dökümlü ve buruşmaya karşı daha dirençlidirler. Çabuk ve iyi nem çekme özelliğinin yanı sıra bu nemi yüzeyinde tutarak kolay kuruma sağlarlar. Yıkama, ütüleme ve kuru temizlemede sararma ve çekme göstermemeleri, astar ile dış giysi arasında oluşabilecek boyutsal problemi azaltır.
Naylon Astarlıklar
Naylon astarlar oldukça sağlam ve hafiftirler. Bunlar en sağlam ve en hafif astarlar olarak nitelendirilebilir. Lifin özelliğinden kaynaklı iyi bir yaylanma, dökümlülük, elastikiyet, buruşmama, çabuk kuruma, yüksek kopma ve sürtünme mukavemeti gösterirler. Ancak sıcağa dayanıklı değildirler. İçerisinde bulunan antistatik materyale göre kiri çekme ve tutma özellikleri değiştirilebilir. Diğer elyaflarla karışım şeklinde kullanıldığında, naylon kumaşa direnç verir.
Polyester Astarlıklar
Polyester elyaf filaman ve tekstüre iplik şeklinde oluşturulur. Filaman halde olanlardan daha parlak ve normal dayanımlı astarlar elde edilir. Tekstüre polyesterden üretilen astarlar ise esnek yapı gösterirler. Polyester astarlar genellikle güçlü ancak elastisitesi az, tatmin edici dökümlülüğe sahip ve kumaş yapısında daha az hava boşlukları bulunan kumaşlardır. İncelik, mukavemet, buruşmazlık, termoplastik özellikleri sebebiyle iyi form tutma yeteneğine sahiptirler. Ancak statik elektriklenme ve boncuklaşma sorunu fazladır. Bu sebeple diğer ipliklerle karışım halinde kullanılır.
Astarlık Kumaşlarda Kullanılan Dokuma Örgüleri
Astarlık kumaşlar genellikle dokuma kumaşlardır. Fakat spor giysilerde yuvarlak ve çözgülü örme makinelerinden elde edilen örme astarlar da kullanılmaktadır. Dokuma astarlıklarda en sık rastlanan dokuma çeşitleri şunlardır;
Bezayağı örgülü dokuma kumaş
Hafif gramajlı astarlıkların dokunmasında en çok kullanılan dokuma tipidir.
Çözgü ve atkı ipliklerinin maksimum bağlantı yapmasından dolayı dayanıklı, kopma ve sürtünme mukavemetleri yüksek kumaşların elde edilmektedir.
Ancak bağlantı sayısının çokluğundan dolayı kumaşın esnekliği ve dökümlülüğü azdır.
Dikiş esnasında ve daha sonraki kullanımlarda, iplik ve dikiş kaymasına izin vermeyen dayanıklı bir kumaş yapısına sahiptir.
Ucuz ve fazla kullanım alanına sahip olmasından dolayı sıkça tercih edilen astar dokuma tipidir.
Dimi örgülü dokuma kumaş
Dimi dokumanın kullanıldığı kumaşların en büyük özelliği, yüzeyindeki diyagonal çizgilerdir.
Bu sebeple, kumaşların esnekliği artmakta ve duruşmalıkları iyileşmektedir.
Bezayağı dokuma kumaşlara göre daha yüksek yırtılma mukavemetine sahiptirler.
Dimi dokumanın kullanıldığı astarlar, kesime ve işlemeye daha uygun ve dayanıklıdırlar.
Üzerlerine yapışan kiri kolay göstermezler.
Daha çok deri giysilerde, manto ve kaban astarlarında kullanılmaktadırlar.
Saten örgülü Dokuma kumaş
Astarlık kumaşların üretiminde en çok kullanılan dokuma tiplerinden birisi de saten dokumadır. Birim örgü raporundaki bağlantı sayısı azdır. Saten dokuma ile üretilen astarlıklar, kaygan, pürüzsüz bir yüzey, parlak görünüm ve dökümlülük gösterir. Parlaklığın sebebi, ipliklerin yüzme yapması sebebiyle ışığı daha iyi yansıtmalarıdır. En fazla 5’li saten dokuma kullanılmaktadır.
Dökümlülüğün iyi oluşundan dolayı palto, mont gibi giysilerde tercih edilir.
Ancak sürtünme dayanımı ve aşınma direnci düşüktür. Zamanla yüzme yapan ipliklerde kopma ve boncuklaşma görülür. İpliklerdeki kaymalar sebebiyle dikim sırasında dikkat edilmelidir. Dikiş kaymasına ve doku kaymasına son derece eğimli bir yapı oluşturdukları için optimum atkı ve çözgü sıklıkları uygulanmalıdır.
Astarlık Kumaşların Özellikleri
Düzgün yüzeyli yapay elyaf filamentleri ve diğer sentetik elyaflardan oluşan ve saten gibi uzun atlama yapan ipliklerin bulunduğu dokuma türlerinde dokunmuş astarlıklarda mevcut iplik ve dokuma özellikleri sebebiyle gevşek ve kaygan bir kumaş yapısı elde edilir. Bu nedenle dikiş kayması, kumaşın doku yapısının bozulması gibi olumsuz sonuçlar ortaya çıkmaktadır. Bunu önlemek için kumaşlarda belirli atkı ve çözgü sıklıklarına ulaşarak dikiş yerlerindeki iplik kaymalarını azaltılmaktadır. Yeterli atkı ve çözgü sıklığına ulaşılamadığı takdirde uygulamada “açma” olarak bilinen ve dikişsiz noktalarda bile zorlama ile ipliklerin kayması ve dokunun bozulması ortaya çıkmaktadır. Düşük atkı ve çözgü sıklıkları kumaşın örtücülüğünü azaltır. Dolayısıyla astardan beklenen en önemli özelliklerden birisi olan, üst kumaşın vücuda temasını önlemek, iç detayları ve hoş olmayan görüntüleri engellemesi fonksiyonunun yerine getirilememesine sebep vermektedir.
Astarlarda yüzey kayganlığı ve parlaklığı, kumaşın kirlenme süresinde ve dayanımında, temizlenmesinde ve sağlamlığında önemli rol oynar. Özellikle kaygan astarlar, kullanım sırasında kullanıcıya giysiyi kolay giyip çıkarma ve diz, omuz gibi eklem yerlerindeki hareketi yayarak üst kumaş formunu muhafaza etmektedir.
Kayganlığın en büyük zorluğu kesim esnasında yaşanmaktadır. Kaygan olmayan ve yüzeyi pürüzlü astarlar ise kullanım esnasında toplanmalar yapmaktadır. İpliği oluşturan elyafların tipi, inceliği, doku yapısı ve terbiye işlemleri astarlık kumaşların parlaklığını belirlemektedir. Sentetik lifler kimyasal bileşimlerine bağlı olarak mat, yarı mat ve parlak gibi farklı derecelere sahiptirler. Bağlantı noktalarının az olduğu saten dokuma kullanıldığında kumaşın parlaklığı artmaktadır. Üçgen kesitli trilobal polyester iplikler ışığı fazla yansıttıklarından dolayı sıkça kullanılmaktadırlar. Terbiye işlemleri sırasında, özellikle ön fikse ve aprede mümkün olan yüksek sıcaklıklara çıkılması parlaklığı arttırmaktadır.
Astarlık kumaşlarda renk uyumu, astarın dış kumaş rengi ile uyumlu olması ve astarın kendi içindeki renk uyumu açıdan incelenebilir. Açık en boyama prosesinde, kumaşın kenarlarına doğru boyanın daha az alınması ya da hiç alınmaması durumlarında astarın kendi içindeki renk uyumsuzluğu karşımıza çıkar. Kumaş üzerindeki renk varyasyonlarının en önemli sebepleri;
- Kumaşın yapısı ve içerdiği nem,
- Çözgü yoğunluğu, kenar kalınlığı ve ağırlıktaki varyasyonlar,
- Makinenin yetersiz basıncı, gerilim farkları ve sıcaklık dağılımı,
- Boya seçimi, sıcaklık kontrolü ve işlem süresi,
- Çevre şartları, fikse ve yıkama şartlarındaki değişimlerdir.
Rengin, yıkama, temizleme, sürtünme, ter ve ışık haslıkları diğer önemli noktalarıdır. Düşük haslık değerleri, terleme ve yıkama sırasında rengin akıp üst kumaşı boyanmasına neden olmaktadır.
Astarlık kumaşların, giysinin kullanım süresine uygun bir şekilde eskimesi beklenir. Ancak, bu seçilen astar tipinin yanı sıra giysinin kullanım şekli ve amacına da bağlıdır. Örneğin, çok sık kuru temizleme yapılan bir giysinin, dış kumaşına uygun kimyasal maddeler, astara ve astar dikişine zarar verebilir. Ayrıca, gevşek dokunmuş, hatalı iplikler içeren astarlıkların kaplama yapılarak kalınlaştırılması ve özelliklerinin iyileştirilmesi sağlanabilir.
Astarların yapıldığı iplik özellikleri, iplik sıklıkları ve dokuma yapısı kullanım sürecinde astarların karakteristiklerini koruyabilmelerine etki etmektedir. Örneğin, bezayağı bir astarlık kumaş, satenden daha dayanıklıdır. Polyester bir astarda artan iplik sıklığı, kıvrımı arttırdığı için kumaş mukavemetini bir noktadan sonra olumsuz yönde etkileyecektir.
Astarlık kumaşlarda yıkama ve kuru temizleme sonucunda oluşabilecek çekme ve sarkma miktarının kabul edilebilir oranlarda olması çok önemlidir. Astarın istenilenden fazla çekmesi durumunda dış kumaşta büzülme meydana gelir. Astarın sarkması durumunda ise, astarın etek ucu ve kol ağzından dışarıya çıktığı görülür. Bu durum, dış kumaş ile astarın yıkama ve temizleme özelliklerinin uyumunu ne denli önemli olduğunu bir kez daha gözler önüne sermektedir. Genellikle sentetik astarlarda fiksaj ve dokumada gerilimin düşürülmesi ile, selüloz bazlı astarlarda ise su çekme özelliğinin azaltılması ile boyutsal stabilite sağlanmaya çalışılmaktadır.
Buruşmazlık, bir astardan, kullanım esnasında beklenen en önemli özelliklerden birisidir. Önemli olan kullanılırken buruşan astarın, basınç ortadan kalktıktan sonra eski haline dönme hızı ve miktarıdır. Selüloz bazlı elyafların daha çok buruştuğu bilinmektedir.
Buruşmazlık özelliği, iplik özellikleri, terbiye koşulları ve dokuma yapısına da bağlıdır.
Lifleri keten; pamuk, viskon, asetat, naylon, polyester ve yün diye sıralarsak, baştan sona doğru buruşma eğilimi düşecektir. Astarlık kumaşlarda kullanılan uzun stapelli iplikler astarın buruşma eğilimini azaltırlar. Dokuma sıklığının artması ve ipliğe büküm verilmesi de buruşmayı azaltır. Ancak buruşmazlık özelliğinin arttırılması, dikim sırasında bazı zorlukları beraberinde getirir. Bu sorunlar terbiye işlemleri esnasında, sıcaklık ve basınç ile azaltılmaya çalışılmaktadır.
Bir astarın en uygun sürtünme dayanımı, kullanım esnasında karşılaşabileceği maksimum gerilme veya baskıya karşı koyabileceği noktadır. Özellikle gevşek yapılı astarlarda tespit edilen gerilim kuvvetleri ile sürtünme dayanımlarına mutlaka uyulmalıdır.
Sürtünme dayanımı, giysinin görüntüsünün bozulmaması açısından son derece önemlidir. Ancak, kol ağzı, etek ucu ve yakalarda sürtünmeden dolayı, astarlık kumaşın iplik konstrüksiyonu ve doku yapısına bağlı olarak pürüzlenme meydana gelebilir. Saten dokumada bu durumun oluşma olasılığı daha yüksektir. Aşınan elyafların kumaş yüzeyinde boncuklaşması sonucu kötü bir görüntü ortaya çıkmaktadır ve sentetik elyaflarda bunların temizlenmesi oldukça zordur.
Elyaflar naylon, polyester, pamuk, rayon, asetat diye sıralandığında, baştan sona doğru aşınma dayanımı düşer. Bu nedenle uygulamalarda asetat ve rayon, genellikle polyesterle, nadiren de naylon ile birlikte aynı astarlık kumaşlarda kullanılır. Bu durum kumaşa bir çift renk efekti sağlamaktadır.
Statik elektriklenme kumaş yüzeyindeki nem miktarına ve sürtünmeye bağlıdır.
Sentetik liflerde (rayon ve asetat hariç) nem miktarının azlığı havadaki elektrik yükünün daha fazla çekilmesine ve dolayısıyla bu liflerden yapılan astarların daha fazla elektriklenmesine sebep olmaktadır. Bu elektrik yüklenmesinin artması, giysinin kullanıcı üstüne yapışmasına, potluğa ve sertliğe yol açar. Özellikle sentetik astarlarda görülen bu durum, astarın kir ve tozu çekmesine ve dolayısıyla astar renginin değişerek parlaklığın azalmasına, kullanıcının rahatsız olmasına ve astardan istenilen fonksiyonların gerçekleşmemesine neden olur.
İnsan vücudunun sıcak ve soğukta rahat etmesi için nemin vücuttan dışarıya çıkması gerekir. Bu sebeple, özellikle vücutla temas eden astarın nemi çekmesi ve dışarıya iletiminin oldukça iyi olması gerekir. Aksi halde rahatsızlık hissi verecektir.
Astarın nem çekme özelliği
dokuma esnasında kullanılan dokuma türü, elyaf tipi ve uygulanan terbiye işlemleri ile ilgilidir. Kesik elyaflı, viskon astarlardaki nem çekme özelliği, polyester gibi filament ipliklerden oluşan astarlardan daha iyidir.
Ayrıca gevşek yapılı astarlar, sık dokunanlara göre daha çabuk nem alır ve verirler.
Bitim işlemleri prosesinde elyaflara iyi bir nem çekme özelliği kazandırılmalıdır.
Astarların genellikle dış kumaştan daha yumuşak olması istenir. Bunun nedeni ise vücut ile temas halinde olmasıdır. Bunun için de kullanılan iplikler aşırı bükümlü ve kalın olmamalı, genellikle ince iplikler tercih edilmelidir. Kullanılan iplik türü ve özellikleri açısından, asetat astar, polyester astardan daha dökümlüdür. Rayon astarlıklar ise, çok iyi döküm ve yumuşaklığa sahip olmalarına rağmen, genellikle daha gramajlı ve kalın olmaktadırlar. Boncuklaşma eğilimi fazla olduğundan dolayı rayon mutlaka polyester veya naylon ile karıştırılmalıdır.
Astarın Giysiye Kazandırdığı Özellikler
Astarlık kumaşlar, üst kumaşın özellikleri ile gösterdiği uyuma bağlı olarak, ürünün bütününe bazı önemli özellikleri kazandırabilirler. Giysiden beklenen konfor, dayanma süresi ve kullanım rahatlığı ile ilgili özellikler şunlardır;
- İmalat sırasında oluşabilecek iç yapı hataları ve detaylarını kapatarak esas kumaşın oluşturduğu açık kenarları kapatır.
- Detay ve dikişleri kapattığı için daha temiz çalışmayı ve dolayısıyla daha fazla işçilik maliyetini ortadan kaldırır, giysiye temiz bir görünüm sağlar.
- Kullanım esnasında, özellikle sürtünme katsayısı yüksek bir kumaş ile yapılmış giysilerde, kolay giyilip çıkarılma rahatlığı sağlar. Ayrıca giysinin kenarlarına takılma sorunu ya da ceplerin dönmesi gibi problemler minimize edilmiş olur.
- Giysinin, kullanıcı hareketleri ile çok fazla esnemesini ve bollaşmasını engelleyerek stabil bir yapı oluşmasına yardımcı olur.
- Dış kumaşın direkt vücut ile temasını engeller.
- Giysinin dikişlere takılarak ya da insan tenine değerek terden etkilenmesi gibi sorunları ortadan kaldırarak, mamulün kullanım ömrünü uzatır.
Astarlıklarda tüketiciyi etkileyen önemli özelliklerden birisi de dökümlülüğüdür. İstenen özelliklere göre; gevşek, kıvrak, sert, akıcı ya da kırılgan bir yapı taşıyan astarlıkların, dokununca hoş duygular yaratan, yumuşak kıvrımlar oluşturan, yoğunluğu hissedilebilen, esnek, kolay dikilebilen ve kullanıcıda rahatsız edici etkiler uyandırmayan özelliklere sahip olması gerekmektedir. Ancak zaman içinde kullanım ve dış giysi kumaşının yıkanması ve temizlenmesinde uygulanan yöntemler ile astarlar değişerek, kumaşın kimyasal anlamda yeni bir yapı kazanmasına, fiziksel olarak görünüşünün değişmesine sebep olmaktadır.
Antep Kutnu Kumaşı, Gaziantep’te yüzyıllardır üretilen ve kullanılan genellikle çözgü sateni veya bez ayağı örgü ile dokunan, boyuna çizgili desenlerden oluşan bir tür atlas kumaştır. Çözgüsü ince ipek, atkısı pamuk ve ipek karışık atılmış, çoğunlukla yollu bir kumaştır. Zamanla çözgüsü suni ipek (floş) iplik, atkısı pamuk iplik kullanılmaya başlanmıştır.
Kumaşın atkı sıklığı ve çözgüsüne göre:
- Çözgü tel sayısı 4000-5000 arası olan, örgüsü atlas saten olan kumaşlar “kutnu kumaş”,
- Çözgü tel sayısı 3000-4000 arası olan; örgüsü bez ayağı, düz çizgili bağlama batik motifli olan kumaşlar “meydanîye kutnu kumaş”,
- Çözgü tel sayısı 2000-3000 arası olan; örgüsü bez ayağı, düz çizgili ve bağlamalı batik tekniği ile kendiliğinden oluşan desenli kumaşlar, “alaca kutnu kumaş” olarak adlandırılmaktadır.
Renkli çözgülerin oluşturduğu boyuna çizgili yolların genişlikleri, renkleri ve desenlerine göre aşağıdaki çeşitler bulunmaktadır.
- Hindiye Kutnu
- Çiçekli Furş
- Çiçekli Mecidiye
- İnce Kalem Meydanîye
- Kemha Kutnu
- Çiçekli Kırmızılı Furş
- Düz Mecidiye
- Müflüs
- Mercan Kutnu
- Çiçekli Şahiye
- Sultan
- Kemha
- Şahiye Kutnu
- Çingene
- Yeşil İnci
- Şaliye
- Kerasi Kutnu
- Furş
- Zefir
- Eli Şalşapik
- Vişneli Furş
- Bayraklı Mecidiye
- Sarı Meydanîye
- Elvanlı Kutnu
Çözgü ipliklerinin bağlama batik tekniği ile renklendirilmesinden dolayı kendiliğinden oluşan desenlere göre de Antep Kutnu Kumaşı aşağıda belirtilen şekilde isimlendirilmektedir.
- Sedefli Bağlama Kutnu
- Zincirli Kutnu
- Vişneli Darıca Kutnu
- Beyaz Taş Kutnu
- Sarı Taş Kutnu
- Bağlamalı Darıca
- Bağlamalı Furş Kutnu
- Mehtap Kutnu
- Bağlamalı Mehtap
- Bağlamalı Sarı Tas
- Bağlamalı Sedefli
- Bağlamalı Zencirli
- Beyaz Tas
Ayrıca farklı isimler ile adlandırılan ve burada belirtilmeyen fakat aynı üretim tekniği ile üretilen kutnu kumaşlarda bulunmaktadır.
Antep Kutnu Kumaşı’nın özellikleri:
- Çözgü adı verilen dikey ipliklerde, ilk dönemlerde ince ipek kullanılmış olup son dönemde ise 100, 120, 150 denye numaralı suni ipek (floş) ipliği kullanılmaktadır.
- Atkı adı verilen yatay ipliklerde 20/NE iki kat pamuk ipliği kullanılmaktadır.
- Haşıl hammaddesi olarak kayısı ağacından elde edilen doğal kitre zamp reçine kullanılmaktadır.
- Renkli çözgülerin oluşturduğu boyuna çizgili desenlerden oluşmaktadır. Bu çizgilerin oluşturduğu yolların genişlikleri, renkleri ve desenleri farklılık göstermektedir.
- Çözgü ipliklerinin bağlama batik tekniği ile renklendirilmesinden dolayı kendiliğinden oluşan desenler bulunmaktadır.
- Kullanılan ipliğin kalınlık ve inceliklerine göre Antep Kutnu Kumaşların 1 cm deki atkı tel sayısı 10-12, 1 cm deki çözgü tel sayısı 56-70 arasında değişmektedir.
- Antep Kutnu Kumaş’larda kullanılan örgüler, genellikle çözgü sateni veya bez ayağı olup, yer yer rips örgü de kullanılmaktadır.
Antep Kutnu Kumaş, yöre insanının geleneksel giysilerinde, halk oyunları kıyafetlerinde ve ayrıca günlük hayatta kullanılan fular, yelek, gömlek, kravat, çanta ve benzeri giyim eşyaları ile perde, döşemelik kumaş ve benzeri dekorasyon ve süs eşyalarının yapımında kullanılmaktadır.
Ürünün Üretimi Antep Kutnu Kumaşı’nın dokuma öncesi, dokuma ve dokuma sonrası işlemlerinin aşamaları aşağıdaki şekilde gerçekleşmektedir.
1. Söküm İşlemi:
Sökücüler tarafından yapılan söküm işlemi yaklaşık 16 m² lik bir alana kurulmuş olan “devere” adındaki çözgü dolaplarında yapılır. Çözgü dolabı dört kanattan oluşur ve kanatlar arasındaki mesafe 1,8 m dir. Dört köşe olarak yapılan dolabın çevresi 7,2 m dir. Çözgü iplikleri bobinlerden sağılarak “devere” adı verilen çözgü dolaplarına sarılır. Deverede, dokunacak kumaşın boyuna göre ve istenilen çözgü tel sayısına göre sarım işlemi yapılır. Sarım işlemi bittikten sonra çözgü ipliklerinin çözülmesi esnasında ipliklerin bozulmamasını ve karışıklığını önlemek için “bağlık(çapraz)” denilen ipliklerle bağlanır ve çile haline getirilir. Hazırlanan çilelere “şak” adı verilir.
2. Boyama İşlemi:
Söküm işleminden sonra, hazırlanan çilelerin boyanması işlemine geçirilir. Boya maddesinin hazırlanması için büyük bir kazana 200 ile 800 litre kadar su konulur. Rengin tonuna, açıklık ve koyuluğuna göre 50 ile 300 gram arası boya maddesi ilave edilir. Boya maddesi ilave edildikten sonra kazana soda ve tuz katılarak boyamaya hazır hale getirilir. Bir renk için boyama işlemi 30 ile 45 dakika arasında gerçekleşmektedir. Boyamacılıkta kök boyalar kullanılmakta iken artık günümüzde genellikle tercih edilen direkt boyalar kullanılmaktadır. Boyamacılıkta ayrıca bağlama batik boyama tekniği de kullanılmaktadır. Bağlama batik boyama tekniğinde ise desenin önceden çizilmesi ve bilinmesi koşulu ile iplikler üzerinde her renk ve hareket için grup bağlamalar yapılmaktadır. Yalnızca en koyu renk ile boyanacak kısımlar açık bırakılır. Daha sonra koyudan açığa doğru bir sıralama izlenerek boyama yapılır. Her boyaya batırmada o boyanın renginde boyanması istenen kısımların üzerindeki bağlar çözülür. Bir önceki boyada üzeri sıkıca sarılı olduğundan boyanmamış olan bu kısım üzerindeki bağlar çözüldükten sonra girdiği boyanın rengini alır. İşlem istenilen renkler elde edilene kadar bu şekilde her ıslatmadan sonra bağlı kısımlar açılarak sürer. En son en açık renklere batırılır.
3. Mezek İşlemi:
Çilelerin boyama işleminden sonra mezek işlemine geçilir. Mezek işlemi haşıllama, elle açma-tarama ve kavuk olmak üzere üç aşamadan oluşmaktadır. Haşıllama işleminde, haşıl maddesi olarak kayısı ağacından elde edilen doğal kitre zamp reçine kullanılarak boyalı veya boyasız çözgü ipliklerinin daha sağlam olması, dokuma esnasında iplik kopmalarının önlenmesi ve aynı zamanda ipliklerin parlaklık kazanması sağlanır. Daha sonra haşıllanan çözgü iplikleri duvara çakılı olan iki çubuk arasına gerilerek haşıllanmış çözgü ipliklerinin aralarını açmak ve düzgünleştirilmesi işlemi yapılır. Haşıllanmış, elle açma-tarama işlemi yapılmış olan çözgü iplikleri 50 cm uzunluğundaki “milef” adı verilen tahta sopalara sarılır. Tahta sopalara sarılma işlemine “kavuk” adı verilir. Hazırlanan kavukların nemli kalması ve haşıl maddesinin ipliğe iyi nüfus etmesi için naylon torbalara konularak 4 ile 24 saat arasında dinlendirilir.
4. Taharlama Öncesi:
Hazırlanan kavuklar, levent adı verilen makaralara sarılarak dokuma tezgahına verilir.
5. Taharlama:
Çözgü iplikleri tek tek gücü tellerinin üzerindeki küçük gözeneklerden geçirilir. Armürlü ve jakarlı tezgahlarda kullanılan gücü telleri metalden olup; kamçılı el tezgahlarında, pamuk ipliğinden hazırlanmış gücü telleri kullanılmaktadır. Gücü tellerinden geçirilen iplikler Antep Kutnu Kumaşı’nın deseni ve sıklığına göre belirlenen tarak numarasına göre hazırlanan tarak dişlerinden üçerli, dörderli, beşerli, altışarlı teller geçirilir.
6. Atkı İpliğinin Hazırlanması:
Atkı ipliği olarak genelde pamuk ipliği kullanılır. Pamuk ipliği iki kat olarak kullanılmaktadır. Kelep halindeki pamuk ipliği haşıllanması için mısır, arpa, buğday nişelerinden elde edilen sıvı maddeye batırılarak nişelenir. Daha sonra sıkılarak ve kurutularak bobin makinelerine hazır hale getirilir. Bobin sarma makinelerinde kullanılacak olan atkı iplikleri masuraya sarılır. Masuranın mekiğe yerleştirilmesinin ardından Antep Kutnu Kumaşı dokunmaya başlanır.
7. Dokuma İşlemi:
Geçmişte ahşaptan yapılmış kamçılı çekme tezgâhta mekikle dokuma tekniği kullanılarak dokunan Antep Kutnu Kumaşı, günümüzde daha gelişmiş armürlü ve jakarlı tezgahlarda dokunmaktadır.
8. Bitim İşlemi:
Antep Kutnu Kumaşı dokunduktan sonra tavlama ve nişeleme, cendereleme ve mengeneden geçirme işlemlerine tabi tutulur. Tavlama ve nişeleme işlemi, Antep Kutnu Kumaşı’nı haşıl maddesi ile nemlendirme işlemidir. Su ve nişasta ile hazırlanan madde kumaşa serpilir. Serpme işlemi çalı süpürgesiyle yapılır. Bu maddenin kumaşa işlemesini sağlamak için kumaş katlanır ve üzerine ağırlık konularak 4 ile 24 saat arasında dinlenmeye bırakılır. Bir gün dinlendirilerek nemi ayarlanan kumaş cendere makinesine verilir. Cendere bir çeşit ütüleme işlemi yapar. Silindirler birbirine ters yöndedir. Silindirlerden oluşan cenderede kumaş sıkışarak basınç altından geçerken yüzeyi parlar ve iplikler ezilerek doku gözenekleri kapanır. Cenderedeki kumaş tek katlıdır. Ancak bazı zamanlarda kumaşlarda hareli görüntüler yapılır. Bu görüntü için de kumaş nemli ve ikiye katlanmış halde cendereye konulur. Böylece kumaş üzerinde bazı yerlerde parlak bazı yerlerde de mat hareli yüzeyler oluşur. Son işlem olarak Antep Kutnu Kumaşı mengeneden geçirilir. Mengenede birkaç top kumaş katlanıp üst üste yığılarak basınç altında bir gün sıkıştırılarak dinlendirilir. Bu şekilde kumaşa düzgünlük ve parlaklık verilir. Belirlenmiş Coğrafi Alanda Gerçekleşmesi Zorunlu Olan Özellikler Antep Kutnu Kumaşı’nın kendine has dokunarak işlenmesi, örgüsü ve boyanması işlemleri, babadan oğla geçen üretim tekniğine ve bu tekniğe göre çalışan ustaların el emeğine dayalı olarak gerçekleştirilmektedir. Dolayısı ile Antep Kutnu Kumaşı’nı üretmek için yılların birikimini almış büyük beceri ve ustalık gerekmektedir.
Antep Kutnu Kumaşı’na özgü olan;
Renkli çözgülerin oluşturduğu boyuna çizgili desenleri, genişlikleri ve renkleri oluşturarak istenilen kumaşı yapmak,
Çözgü ipliklerinin dokumada alacağı şekil, desen ve motif düşünülerek hesap edilip bağlama batik tekniği ile renklendirilmesi ve renklendirilmesinden dolayı kendiliğinden oluşan şekilleri, desenleri ve motifleri yapmak, tamamen yetişmiş ustaların becerisine ve el emeğine dayanmaktadır. Bu nedenle özellikle “bağlama batik boyama” ile kumaşın dokunması işlemlerinin Gaziantep ili sınırlarında gerçekleştirilmesi gerekmektedir.
Dokumada, kumaş oluşum prensibi yıllardır değişmemesine karşın kullanılan metotlar ile dokuma makinelerinin tahrik ve kontrol şekilleri zaman içerisinde değişikliğe uğramıştır. Yirminci yüzyılın sonlarında değişim hızı sürekli olarak artmış ve makinelerin üretim miktarını belirleyen atkı atma hızları 1950-2000 yılları arasında yaklaşık 10 kat artmıştır. Üretim hızları artış hızı sürekli artarak günümüze kadar gelmiştir. 21. Yüzyılın başından bu güne kadar geçen süre de ise artış hızı sürekli artarak 1950-2000 yılları arasındaki 10 kat artışa yakın bir değere ulaşmıştır. Önceden emek yoğun bir endüstri kolu olan dokuma endüstrisi sektörü artık modern teknolojilerle sermaye yoğun bir endüstriye dönüşmüştür.
Bir kumaşın dokunmasındaki temel işlemler şunlardır;
1) Ağızlık açma, yani atkı ipliğin çözgü iplikleri arasından geçirilmesini sağlamak için desene göre ipliklerin iki veya daha fazla tabakaya ayrılması işlemi,
2) Atkı atma (atkı kaydı),
3) Tefe vurma (tefeleme), yani ağızlığa yatırılan atkı ipliğini kumaş çizgisine kadar taşıyıp kumaşa dahil etmektir (bir önceki atkı atıldıktan sonra kumaşın sona erdiği çizgi).
Atkı ve çözgü ipliklerinin beslenmesi ile dokunan kumaşın sarılması için de gerekli üniteler makine üzerinde mevcut olmalıdır. Çözgü ipliği genellikle çözgü levendi üzerinden beslenirken atkı ipliği masura (sadece mekikli tezgâhlar için) veya konik bobinler üzerine sarılarak beslenir. Atkı atma sistemi ne olursa olsun tek fazlı dokuma makinelerinin çoğu benzer mekanizmalar ve arka köprü ile göğüs köprüsü arasında yatay bir çözgü hattı kullanılmaktadır.
Yatay çözgü hattı en yaygın olarak kullanılmasına rağmen diğer başarılı çözgü hatları da geliştirilmiştir.
Dokuma tezgâhları her tefeleme işleminden sonra bir sonraki atkı için ağızlık oluşumunu takiben yeni bir atkının ağızlığına tüm kumaş eni boyunca yatırıldığı ve bu işlemlerin her makine devrinde tekrar ettiği tek fazlı ve aynı anda birden fazla dokuma işlemi fazının mevcut olduğu ve eş zamanlı olarak birden fazla atkı atımının gerçekleştirildiği çok fazlı olarak iki guruba ayrılabilir.
Tek fazlı dokuma makineleri atkı atma sistemlerine göre alt guruplara ayrılırken çok fazlı dokuma makineleri ağızlık oluşturma metotlarına göre sınıflandırılır.
Bir dokuma makinesinin başarılı ve verimli bir şekilde çalıştırılması için iyi kalitede çözgü ipliklerine ihtiyaç vardır.
ÇÖZGÜ HAZIRLAMA
Dokuma işleminin başarısı, dokuma makinesine takılan çözgü levendinin hazırlama kalitesine bağlıdır. Çünkü çözgüdeki her bir hata ya makineyi durdurup düzeltme gerektirecek ya da dokunmakta olan kumaşta hataya sebep olacaktır. Bir kumaş dokunmadan önce çözgü ipliklerinin sarıldığı leventler hazırlanmak zorundadır.
Çok kalın çözgü iplikleri için veya çözgü hazırlama özellikleri değiştirilmeksizin filament ipliklerden kumaş dokunabilmesi durumunda her dokuma makinesinin arkasına yerleştirilebilen bir cağlık ekonomik olarak kullanılabilir.
Bu yaklaşım ile sık sık levent değişimi önlendiği için dokuma randımanı artırılır, ancak çok fazla yere ihtiyaç duyulur. Çözgü ipliklerinin büyük bir çoğunluğu için özellikle haşıllanmış iplikler için çözgü levendi hazırlamak ve dokuma makinesinde kullanmak daha ekonomik olmaktadır Çoğu çözgü hazırlama sisteminin amacı dokuma makinesinde ihtiyaç duyulan çözgü ipliklerini bir levende birleştirmek ve çözgüyü, tüm çözgü telleri sürekli olarak mevcut olacak şekilde ve çözgülerin elastikiyetlerini sarıldıkları haldeki değerlerinde muhafaza ederek dokuma makinesine beslemektir. Bu işlem yapılmadan önce iplikler konik bobinlere sarılmalı, çözgü levendine aktarılmalı ve en son olarak da dokuma levendine aktarılmadan önce haşıllanmalıdır.
Haşıl işleminin amacı dokuma makinesinde karmaşık zorlamalara maruz kalan çözgü ipliklerinin dayanımını artırmak amacı ile çözgüleri koruyucu bir tabaka ile kaplamaktır. Bazı kalın katlı iplikler ile yüksek dayanıma sahip iplikler haşıllanmadan da dokunabilir.
AĞIZLIK AÇMA
Bir kumaş, ister bir el tezgâhında ister en modern yüksek hızlı çok fazlı dokuma makinesinde dokunsun, tefeleme ve kumaş oluşumundan önce atkının atılabilmesi için ağızlık açılması zorunludur.
Ağızlık temiz olmalıdır, yani gevşek çözgü iplikleri veya yüzeyi tüylü iplikler veya birbirleriyle tutuşan çözgüler atkı ipliği veya atkı taşıyıcının geçişini engellememelidir. Bu engelleme olmaksızın atkı ipliği atılamazsa ya sorunu düzeltmek için makine duracaktır. Bir çözgü kopmuş veya hasar görmüş olabilir ya da hatalı kumaş deseni oluşabilir.
TEK FAZLI DOKUMA MAKİNELERİNDE AĞIZLIK AÇMA
Tek fazlı dokuma makinelerinin büyük bir çoğunluğunda atkı kaydı başlamadan önce alt ve üst çözgü tabakaları ayrılarak ağızlık oluşturulur ve atkı tüm çözgü eni boyunca ağızlığa yatırılana kadar çözgülerin ağızlıktaki konumu değiştirilemez.
Ağızlık açma mekanizması çözgü ipliklerini, örgü raporu tarafından belirlenen sırada yukarı veya aşağı hareket ettirmek için kullanılır. Dokuma esnasında çözgü ipliklerinin iyi bir şekilde ayrılmasını sağlamak ve bitişik ipliklerin birbirleri ile tutuşmalarını (birbirlerine yapışmalarını) engellemek için çözgü tabakalarını oluşturan iplikler birbirine göre bir miktar kaydırılabilir. Ancak atkı kayıt bölgesinde atkı geçişini engellemeyecek şekilde bir açıklığın muhafaza edilmesi zorunludur. Belirli bir dokuma makinesi için seçilen ağızlık açma mekanizması bu makinede ön görülen desene bağlıdır. Ağızlık açma mekanizmaları genellikle pahalıdır ve desenlendirme yeteneği ne kadar büyük olursa ağızlık açma mekanizması da o kadar pahalı olacaktır. Bazı dokuma makinelerinde bu makineye takılabilecek ağızlık açma mekanizmalarını belirleyen teknik sınırlamalar da vardır. Kranklı, kamplı veya armürlü ağızlık açma mekanizmaları kullanıldığında çözgü iplikleri çerçevelere takılan güçlü gözlerinden geçirilir ve çerçeveler tarafından yukarı-aşağı hareket ettirilir. Bir çerçevedeki tüm gücüler birlikte hareket ettirilir ve bu çerçeve tarafından kontrol edilen tüm çözgüler bundan dolayı aynı şekilde kaldırılır.
Örgü raporu ihtiyaç duyulan minimum gücü sayısını belirler. Bir çerçevedeki gücü sayısının çok fazla olmasını önlemek için aynı hareketi yapan çözgüler aynı hareketi yapan birden fazla çerçeveye dağıtılır. Bez ayağı kumaş dokumak için örneğin 2, 4, 6, 8 çerçeve kullanılabilir. Bu durumda çözgüleri her atkıda çerçevelerin yarısı kaldırılır iken diğer yarısı indirilir.
Kranklı ağızlık açma mekanizmaları genellikle 8 çerçeve ile, kamlı 10 veya 12 çerçeve ve armürlü ağızlık açma mekanizmaları ise 18 veya 24 çerçeve ile sınırlıdır.
Bir desen için gerekli hareket raporu 24 çerçeve kullanımı ile elde edilmezse her bir çözgü ipliğinin ayrı ayrı kontrol edilebildiği jakarlı ağızlık açma mekanizmaları kullanılmak zorundadır.
Kranklı ağızlık açma mekanizması mevcut olan en basit ve en pozitif olanıdır. Sadece bez ayağı örgüde kumaş dokumak için kullanılabilir. Bu mekanizma ucuz, muhafazası ve bakımı kolay ve birçok yüksek hızlı dokuma makinesinde atkı atma hızlarını % 10 kadar artırır. Çok yönlü olmaması nedeniyle yaygın olarak kullanılmamaktadır. Bununla birlikte kumaşların büyük bir çoğunluğunun bez ayağı örgü ile dokunmasından dolayı birçok endüstriyel kumaş için özellikle faydalıdır. Yüksek hızlı modern dokuma makineleri ile kullanılan kamlı ağızlık açma mekanizmaları ya oluklu kam ya da eşlenik kamlara sahiptir. Çünkü bu kamlar çerçevelerin pozitif olarak kontrolünü mümkün kılar. Bununla birlikte negatif profile sahip kamlar hafif ve orta gramajlı kumaşların dokunmasında hala yaygın olarak kullanılmaktadır. Kam profili, örgü raporundan elde edilen hareket planına göre istenilen çerçeve hareketlerini verecek şekilde tasarlanır.
Çerçeveleri kontrol etmenin üçüncü bir yolu ise armürlü ağızlık açma mekanizması kullanmaktadır. Armürlerin en büyük avantajı dokunabilen desenin rapor büyüklüğüne pratik olarak bir sınır getirmemesidir. Buna karşılık kamlı ağızlık açma mekanizmalarında sekiz veya on atkıdan daha büyük örgü raporlarının eldesi pahalı ve zordur. Armürleri çok sayıda çerçeve için üretmek kolaydır. Armürler silindirler veya baklalar içeren desen zincirleri tarafından kontrol edilirler. Desen baklaları armürdeki çerçeve kaldırma mekanizması için seçme işlemi gerçekleştirilir. Uzun hareket raporları için metal zincirler veya ağır tahta baklalar yerine delikli karton veya plastik kartlar kullanılmıştır. 1990’ lı yıllarda elektronik armürler mekanik armürlerin yerini almış ve bu sayede bir desen hazırlamak için olan süre çok kısalmıştır. Elektrik armürlerin gelişmesine müteakip kamlı ağızlık açma mekanizmaların popülerliği azalmıştır. Çünkü yüksek hızlı dokuma makineleri için kamlar pahalıdır. Örgü yapısı veya sık sık desen değişim gereksinimden dolayı çok sayıda kamına gerek duyulursa armürlü dokuma makinesi almak daha ucuza gelebilir. Ağız açma mekanizmaları hala yoğun bir gelişme içerisindedir. Çerçevelerin ayrı ayrı elektronik kontrolü yakın zamanda kranklı, kamlı ve armürlü makineler arasındaki fiyat farkını azaltabilir. Gelişmelerin ağızlık açma ünitelerini basitleştirmesi, fiyatlarını ve bakımını azaltması ve dokuma makinesini daha esnek hale getirmesi daha muhtemel görünmektedir. İstenilen tasarımları dokumak için armürlerin desenlendirme kapasiteleri yetersiz kalır ise jakarlar kullanmak zorunluluğu vardır. Modern elektronik jakarlar çok yüksek hızlarda çalışabilmekte ve tasarlanan desen üzerine pratik olarak hiçbir sınırlama getirmemektedir. Dokuma makinesi eni boyunca her çözgü ipliği ayrı ayrı kontrol edilebilir ve atkı raporu istenilen uzunlukta olabilir. Jakarlar pahalıdır ve çok fazla sayıda çözgü ipliği gruplar halinde konrolü yerine ayrı ayrı kontrol edilecek ise, jakarlar üzerine takıldığı dokuma makinesi kadar maliyete sahip olur.
ÇOK FAZLI DOKUMA MAKİNELERİNDE AĞIZLIK AÇMA
Çok fazlı dokuma makinelerinin tamamına yakınında eş zamanlı olarak birden fazla atkının atılabilmesi için herhangi bir anda birden fazla dokuma işlemi fazı oluşturulur. Dalga ağızlı dokuma makinelerinde çözgü tabakalarının farklı kısımları herhangi bir anda dokuma işlem fazının farklı kısımlarındadır. Yani makine genişliği boyunca çözgü tabakalarına bakıldığında bir kısmında ağızlık oluşmuşken diğer kısmında ağızlık kapanmış, başka bir kısmında da ağızlık yeni oluşuyor veya kapanıyor konumundadır. Bu durum aynı düzlemde birbirini takiben oluşan ağızlıklar içinde belirli sayıda mekik veya atkı taşıyıcının hareket etmesini sağlar. Mekiklerin açılan dalga ağızlıkları boyunca dairesel bir yörünge üzerinde hareket ettiği dokuma makineleri ‘’yuvarlak dokuma makineleri’’ olarak adlandırılır. Bu makineler, ağır yükleri taşıyacak çuval ve çantalar için yuvarlak polipropilen dokuma kumaşların üretilmesi için yaygın olarak kullanılmaktadır.
ATKI ATMA VE TEFELEME ( TEK FAZLI DOKUMA MAKİNELERİ )
Tüm tek fazlı dokuma makineleri atkı atma sistemlerine göre sınıflandırılırlar.
Tek fazlı atkı atmada ana metotlar;
Mekikli, mekikçikli, kancalı veya su jetli sistemlerdir.
KONVEKSİYONEL ( MEKİKLİ ) DOKUMA MAKİNELERİ
Ağızlık boyunca taşınması için mekiklerin kullanıldığı tezgâhlar ABD gibi yüksek ücretlerin ödendiği ülkelerde dahi 1980’li yıllara kadar dokuma kumaş üretimine hâkim olmuştur. Şimdi birkaç tip özel kumaşın dokunması haricinde kullanılmamaktadır. Buna rağmen çok sayıda otomatik bobin değiştirmeli tezgâhlar hala kullanılmaktadır. Ancak bunlar hızlı bir şekilde mekiksiz dokuma makineleri ile değiştirilmektedir. Mekiksiz dokuma makineleri daha az hata ile kumaş üretmekte, dokuma ve bakım için daha az işçiye ihtiyaç duyulmaktadır. Milyonlarca el tezgâhı Güneydoğu Asya’da yasalar ile korunarak hala çalışmaktadır.
Mekikli bir dokuma makinesinde kumaş üretiminde atkının üzerine sarıldığı masurayı taşıyan mekik makinesinin her iki yanında bulunan vuruş mekanizması ile tezgâhın bir yanından diğer yanına ağızlık boyunca hareket ettirilir. Her atkı için mekik aniden ivme kazanır ve mekik yolu üzerinde uçar. Ağızlık boyunca mekik hareket ederken bir atkılık iplik ağızlığa yatırılır. Diğer taraftaki mekik kutusuna ( yuvasına ) ulaştığında mekik hızlı bir şekilde durdurulmak zorundadır. Her atkı ağızlığa yerleştirildikten sonra tefelenerek kumaşa dâhil edilir. Tarak ve mekik yolu tefeye monte edilerek tefe ile birlikte ileri-geri hareket ettirilir. Mekik ağızlık boyunca hareket ederken çözgü ipliklerinin hasar görmeksizin mekik geçişine imkan vermesi amacıyla tefe çerçevelere yakın konumda olur. Daha sonra ağızlığa yatırılan atkıyı kumaşa dâhil etmek için tefe ileri hareket ettirilir. Atkı atma periyodunun büyük kısmında açık bir ağızlığa olan gereksinim ve tarak ile mekik yolunu üzerinde taşıyan tefenin ağırlığı atkı atma hızına yani tezgâh devrine sınırlamalar getirmektedir. Mekikli dokuma makinelerinin temel zayıflığı, mekik tarafından taşınarak ağızlığa yatırılan küçük atkı ipliği kütlesi ile karşılaştırıldığında mekik ve masura kütlesinin oransız bir şekilde olmasıdır. Mekiğe aktarılan enerjinin sadece % 3’ ü gerçek atkı atmak için kullanılır. Makine hızı üzerine getirilen diğer bir sınırlama ise ağır tefeye salınım hareketi yaptırılması gereğidir. Teorik olarak geniş makinelerde 450 m/dak atkı atma hızlarına ulaşmak mümkün olsa da ticari kullanımda 250 m/dak atkı atma hızını aşan ancak birkaç makine olmuştur. Otomatik olmayan mekikli tezgâhlarda her defasında masuradaki atkı ipliği bitmek üzereyken dokumacı tezgâhı durdurmak ve masurayı değiştirmek zorundadır. Atkının ağızlık ortasında bitmesini ve dolayısıyla onarılması gereken bir kopuk atkının oluşmasını engellemek için masuralar, üzerinde çok az iplik varken değiştirilmek zorundadır. Sanayileşmiş ülkelerde otomatik olmayan ve yarı otomatik mekikli tezgâhlar masuraların otomatik olarak değiştirildiği mekikli tezgâhlarla değiştirilmektedir. Otomatik mekikli tezgâhlarda masuralar makine durdurulmaksızın dokumacının müdahalesi olmaksızın değiştirilir. Makinenin gerektiğinde masura değiştirme işlemini gerçekleştirebilmesi için boşalan masuraların yerine yenileri periyodik olarak magazine yerleştirilir. Magazin doldurucular mekik kutusu yükleyicileri ile değiştirilebilir. Masuralar özel kutular içinde tezgâha getirilir ve bu kutulardan otomatik olarak değiştirme mekanizmasına aktarılır. Masuralar boşaldığında masuralar yerine mekiğin değiştirildiği tezgâhlar çok zayıf iplikler için mevcuttur. Bütün bu metotlar tezgâha getirilmeden önce masuraların sarılmasını gerektirir. Mekikli tezgâhlarda dokunabilen kumaşların gramajı ve eni üzerine pratik olarak bir sınırlama getirilmemiştir. Desene göre birden fazla renk veya tipte atkı atılmasına imkân sağlamak için mekikli tezgâhlara ilave olarak mekik kutuları ve özel mekanizmalar takılabilir. Mekikli tezgâhlar mekiksiz tezgâhlarla karşılaştırıldığında, mekiksiz tezgâhlara göre daha hantal yapıda ve iş gücü isteyen tezgâhlar olduğu görülmektedir.
MEKİKÇİKLİ DOKUMA MAKİNELERİ
Mekikçikli dokuma makineleri ya makinenin iki yanından da sırayla fırlatılan tek mekikçik kullanılır ve iki taraftan atkı besleme sistemine ihtiyaç sahip olup tek taraftan fırlatılan çok sayıda mekikçik kullanılır. Daha sonra bu mekikçikler bir taşıma kayışı veya zinciri ile mekikçiğin fırlatıldığı tarafa getirilir. Tüm mekiksiz dokuma makinelerinin önemli bir avantajı konik bobin üzerindeki atkı kullanılmadan önce tekrar sarılmak zorunda değildir. Bu bir işlemi ortadan kaldırır ve ipliklerin karışma tehlikesini azaltır. Böylelikle atkı ipliğinin üretildiği sırada kullanılması sağlanmış olur.
Mekikli tezgâhlarda ise atkı nispeten kısa uzunluklara bölünerek masuralara sarılır. Bu iplikler daha sonra ters sıradan dokunur. Bu durum bir iplikteki uzun periyodik hataları ortaya çıkarabilir.
Bir Sulzer tipi dokuma makinesinde atkı atımı için atkı bobinden çekilerek atkı freni ve gerdiriciden geçirildikten sonra atkıyı mekikçik tutucusuna yerleştirilen mekikçik besleyicisine iletilir. Mekikçik vuruş elemanından (piker) ayrılmadan önce mümkün olan en fazla enerjiyi mekikçiğe aktarmak için atkı atmada burulma çubuğu sistemi kullanılır. Mekikçiği ağızlıktaki kılavuzlar boyunca hareket ettirip diğer taraftaki mekikçik frenine ulaştırmak için gereken enerjiyi beslemek amacıyla burulma çubuğu (burulma açısı) ayarlanabilir. Sulzer daha güçlü ve atkı atmak için daha fazla zaman ayrılmasına imkân sağlayan daha hızlı tefe vuruşu elde etmek için tarak ve tefe mekanizmasını yeniden tasarlamıştır. 3600 mm enindeki makineler 1300 m/dak. ‘ya kadar hızlarda atkı atabilirken dar mekikli tezgâhlar 1000 m/dak atkı kayıt hızlarında çalışabilmektedir. Ağır kumaşlar kalın ve fantezi iplikler ile 6 renge kadar atkı için mekikçikli dokuma makinesi modelleri mevcuttur. Makinelere her çeşit ağızlık açma mekanizması ile makine performansını ayarlamak ve izlemek için mikroişlemciler takılabilmektedir. Tarak eni arttıkça atkı atma hızı artığından ve geniş mekikçikli dokuma makinelerinde birim genişlik başına yatırım maliyeti azaldığı için bir geniş en makinede yan yana belirli sayıda kumaş dokumak sıkça tercih edilmektedir.
KANCALI DOKUMA MAKİNELERİ
Kancalı tezgâhlar tek veya çift kanca ile çalışabilmektedir.
Tek kancalı makinelerde genellikle sert kanca kullanılmaktadır ve kalın ipliklerden dar kumaşların dokunmasında avantaj sağlamaktadır. Tek kancalı geniş makineler birçok uygulama için çok düşük hızlı kalmaktadır. Tek kancalı dokuma makinelerinde kanca, tezgah eni boyunca hareket eder ve genellikle geri dönüş hareketi esnasında atkıyı tutup ağızlığa yatırır. Sert tek kancanın bir varyasyonu iki fazlı kanca olarak da isimlendirilen iki taraflı çalışan tek kancalı sistemlerdir. Bu sistemler teknik (endüstriyel) kumaşlar kullanılmaz. Kancalı dokuma makinelerinin çoğu her kancanın ağızlığa bir taraftan girdiği çift kanca kullanılmaktadır. Kancalar ortada karşılaşır ve atkı transferi gerçekleşir. Gabler sistemi ilk atkı, makinenin her iki tarafından sırayla atılır. Atkı iki devirde bir kesildiği için her iki tarafta da atkı ipliklerinin U şeklinde bağlandığı kumaş kenarları oluşur.
Bugün üretilen makinelerde Gabler sisteminin yerini Dewas sistemi almıştır. Dewas sisteminde atkı tek taraftan atılır ve her makine devrinde kesilir.
Çift kancalı dokuma makinelerinde esnek veya sert kancalar kullanılmaktadır. Sert kancalı dokuma makineleri diğer atkı atma sistemine sahip makinelerden daha fazla yere ihtiyaç gösterirler. Çift kancalı dokuma makineleri ile dokunan kumaşlar düşük sıklıklı jeotekstil amaçlı kumaşlardan ağır konveyör bantlarına kadar uzanır.
Kancalı dokuma makinelerinde genellikle çift esnek kancalar kullanılır. Bu makinelerde 4600 mm’ e kadar enler mevcuttur ve endüstriyel kumaşlar için daha geniş enlerde özel amaçlar içinde üretilmektedir. Standart makineler nispeten düşük yatırım maliyetine sahiptir ve geniş bir aralıkta hafif ve orta gramajlı kumaşları dokumak için kullanılmaktadır. Sekiz renge kadar atkı renk seçme mekanizması basit ve ucuz olduğu için kancalı dokuma makineleri birden fazla renk veya tipte atkının atıldığı kumaşların dokunmasında ve kısa metrajlı çalışmalar için idealdir.
Döşemelik ve modaya uygun kumaşların dokunmasında yaygın olarak jakarlı ağızlık açma mekanizmalarıyla kullanılırlar. Kancalı tezgâhlar bazı endüstriyel kumaşların üretiminde de kullanılmaktadır.
AKIŞKAN JELLİ DOKUMA MAKİNELERİ
Akışkan jelli dokuma makineleri atkıyı ağızlık boyunca taşımak için hava ya da su kullanılır. Bu sistem atkı atımı için bir atkı taşıyıcı veya kancaya ihtiyaç gösterir. Bundan dolayı çok daha az hareketli aksam ve hareket ettirilecek çok daha az kütle mevcuttur.
İpliklerin büyük bir çoğunluğu hava jetli tezgâhlarda kullanılabilmesine rağmen su jetli dokuma makineleri sadece su itici iplikler için uygundur.
Su jetli tezgâhlarda atkıyı ağızlıkta tüm en boyunca taşıyabilmek için genellikle atkının atıldığı tarafta tek bir düze bulunur. Bu yüzden makine enleri yaklaşık 2 metre ile sınırlıdır.
Hava akışının kontrolü basınçlı suyun akışının kontrolünden daha zor olduğu için tek düzeye sahip hava jetli dokuma makineleri ticari olarak 1700 mm’ ye kadar olan enlerde başarılı olmuştur. Daha geniş makineler için makine eni boyunca düzgün bir atkı ipliği hareketi sağlamak amacıyla tarak enine yardımcı düzeler yerleştirilmiştir. Teorik olarak geniş enli hava jetli makineler üretilebilse de ticari olarak tek en makineler daha caziptir ve makine enleri 3600-4000 mm tarak genişlikleri ile sınırlıdır. Basınçlı havanın üretilmesi pahalıdır ve akışını kontrol etmek zordur. Bu nedenle ya özel hava kanalının ya da özel bir profil ile tarakta oluşturulan kanalın içinden atkıyı taşımak için hava akışının sınırlandırılması zorunludur.
Hava jetli tezgâhlar 1970’li yıllarda büyük miktarlarda ticari kullanıma girdiğinden hızlı bir şekilde gelişmiştir. Bu gün hava jetli tezgahlar dokuma kumaşların büyük bir çoğunluğunu dokuyabilmekte ve nispeten basit kumaşların seri üretimine hâkim durumundadırlar.
Hava jetli dokuma makineleri 3000 m/dak. Atkı hızına ulaşmışlardır. Bu hız herhangi bir tek fazlı atkı atma sistemi ile ulaşılan hızın yaklaşık iki katıdır ve hala yoğun bir gelişme çabası içerisindedir. Hava jetli sistem atılan bir metre atkı başına yatırım maliyeti ile yüksek seviyede rekabet eder durumdadır.
Otomatik atkı onarım sistemine sahip hava jetli dokuma makineleri ana düze ile kumaşın diğer taraftaki kenarı arasında meydana gelen atkı hatalarının büyük bir çoğunluğunu onarabilmektedir. Bu ünite çözgü ipliklerine zarar vermeden kopan atkı ipliğini ağızlıktan uzaklaştırılmakta ve makineyi tekrar çalıştırmaktadır. Makine hatayı belirleyemez ve gideremezse sinyal üreterek dokumacıyı uyarır.
Hava jetli dokuma makinelerinde makine duruşlarının büyük bir kısmını atkı duruşları oluşturduğundan bu sistem dokumacının iş yükünü çoğu durumda % 50’ den fazla azalmaktadır. Bu sistem ile dokunan kumaş kalitesi iyileştirildiği gibi aynı anda birden fazla makinenin durması ile ortaya çıkan kayıp zaman da azaltılmaktadır.
DİĞER MEKANİZMALAR VE TEK FAZLI DOKUMA MEKANİZMALARINDA KULLANILAN AKSESUARLAR
ÇÖZGÜ BESLEME VE ÇÖZGÜ SALMA TERTİBATI ( MEKANİZMASI )
Çözgü iplikleri dokuma makinesine bir veya daha fazla dokuma levendinden beslenir. Özel durumlarda cağlıktaki bobinlerden doğrudan besleme yapılabilir. Çözgü ipliklerinin leventten boşalması esnasında tüm tellerin aynı uzunlukta olmasını sağlamak için çözgüler levende eşit aralıkla ve aynı gerginlikle sarılmalıdır.
Levent çapı arttıkça sarılan çözgü uzunluğu artar ve daha az levent değişimine ihtiyaç duyulur. Ancak daha büyük çözgü gerginlik değişimlerin dengelemek zorunluluktur.
Farklı dokuma makinelerinde değişik çaplarda leventler takılabilir. Endüstriyel (teknik) kumaşlar veya denim gibi kalın çözgü iplikleri kullanılan kumaşların dokunması için daha büyük çapta leventlere gereksinim duyulur. Bu leventler tezgahın arkasına yerleştirilen ayrı bir levent cağlığına yerleştirilir.
Bu tür levent cağlıkları ile 1600 mm çapa kadar leventler kullanılabilir. Levent üzerindeki çözgü genişliği en az taraktaki iplik genişliği kadar olmalıdır.
Çözgü genişliği 2800 mm’yi aşar ise haşıl işlemi ve levent taşımayı kolaylaştırmak için birden fazla çözgü levendi kullanılır. Bir kumaşta birden fazla çözgü levendi kullanılır ise bitim işleminden sonra kumaş hatalarına sebep olan farklılıkları önlemek için leventler aynı koşullar altında hazırlanmalıdır.
Dokuma esnasında farklı leventlerden beslenen çözgü gerginlikleri dikkatli bir şekilde kontrol edilmek zorundadır ve elektronik sensörlerin kullanılması ile bu işlem daha basit hale gelmiştir.
Dokunacak olan kumaş birbirinden büyük oranda farklılık gösteren iplik numaralarında çözgü ipliklerine ihtiyaç gösterir veya çözgünün farklı kısımları birbirinden büyük oranda farklı kıvrım değerlerine sahip ise birden fazla çözgü levendi ile paralel olarak çalışmak gerekir. Bu leventler dokuma makinelerinde üst üste veya arka arkaya yerleştirilebilir.
Dokuma esnasında çözgü salma mekanizması her makine devrinde gerekli oranda çözgü ipliğini dokuma bölgesine besler. Atkı atmadan önce ağızlık oluşurken çözgü ipliklerinin iki veya daha fazla tabakaya kolaylıkla ayrılabilmesi için çözgü salma mekanizması çözgüleri eşit ve düzgün gerginlikte tutmalıdır.
Bu sayede son atılan atkının tefelenmesi esnasında gerekli çözgü gerginliği muhafaza edilmiş olur. Çözgü salma mekanizmaları arka köprünün yer değiştirmesiyle gerginlik ölçülerek mekanik olarak kontrol edilmekte idi ancak artık elektronik sensörler ile gerginlik ölçülür ve çözgü salma ayrı servo motorlarla kontrol edilmektedir.
KUMAŞ ÇEKME TERTİBATI ( MEKANİZMASI )
Kumaş çekme mekanizmaları dokunan kumaşı sabit bir hız ile ileri çekmek için kullanılır. Kumaş çekme hızı, atkı sıklığını kontrol eder ve atkı sıklığı değişimleri ile diğer kumaş hatalarını önlemek için düzenli olmak zorundadır. Dokuma makinelerinin çoğunda kumaş çekme mekanizması dokunan kumaşın kumaş silindirine sarılmasını da kontrol eder. Ağır kumaşların dokunmasında yaygın olarak büyük çaplı kumaş silindirlerinin hazırlanması gerekli ise tezgah gövdesinin dışına ayrı bir kumaş sarma ünitesi yerleştirilir.
OTOMATİK DURDURMA TERTİBATI
İlk grup, çözgü koruma tertibatları, sadece mekikli veya mekikçikli dokuma makineleri için geçerlidir. Bu tertibatlar mekik sıkıştığında makineye zarar verilmesini ve çok sayıda çözgünün kopmasını engeller.
Çözgü durdurma tertibatları, çözgü koptuğunda dokuma makinesini durdurur. Çözgü iplikleri koptuğunda lameller aşağı düşer ve çözgü durdurma tertibatı aktif hale getirilir. Lameller mekanik veya elektriksel çözgü durdurma tertibatlarıyla birlikte kullanılır. Lameller tarafından çözgü ipliklerine hasar verilmemesi için çözgüler düzgün bir şekilde haşıllanmalıdır.
Çözgü iplikleri ile fiziksel teması olmayan elektronik çözgü durdurma tertibatları özellikle ince filamantli iplikler için kullanılmaktadır.
Atkı durdurma tertibatları otomatik mekikli dokuma makinelerinde atkı değiştirme işlemini başlatmak ve atkı atma esnasında atkı ipliği koptuğunda makineyi durdurmak için kullanılır. Otomatik kopuk atkı onarım sistemine sahip hava jetli dokuma makinelerinde atkı durdurma tertibatı atkı onarım işlemini de başlatır.
HIZLI TİP DEĞİŞİMİ
İlk defa Picanol tarafından sergilenen ve şimdi bütün makine imalatçılarının sahip olduğu hızlı tip değişim sistemi (QSC) bir çözgü değişimi esnasında makinenin durdurulması gereken süreyi büyük ölçüde azaltır. Çözgü levendi, arka köprü, çözgü durdurma tertibatı, çerçeveler ve tarak, bu kısımları dokuma makinesinin gövdesinden ayıran bir modüle yerleştirilir.
Bu modül özel bir taşıma ünitesi ile tahar ve iş bağ bölümlerine taşınarak çözgü değişimi için hazırlık yapılır ve tekrar dokuma makinesine getirilir. Böylece normal olarak duran dokuma makinesi üzerinde yapılan işlerin % 90 kadarı çözgü değişim işleminde ortadan kaldırılır ve dokuma makinesi randımanı iyileştirilir. Bu sistem ile taraklar ve çerçeveler daha temiz kalacağından daha iyi makine performansı ve kumaş kalitesi elde edilmiş olur.
MAKİNE GENİŞLİĞİ
Bir dokuma makinesinin tarak eni dokunacak olan kumaşın taraktaki eninden daha geniş veya taraktaki enine eşit olmalıdır. Taraktaki çözgü genişliği kumaş kenar genişlikleri ve yardımcı kenar çözgülerini kapsamalıdır. Makine genişliği bu ender dar ise kumaş bu makinede dokunamaz.
Genel olarak bir makinenin tarak enini artırmak mümkün değildir. Mevcut makine eninin üzerine çıkılamazken daha ağır kumaşları dokumak genellikle mümkündür. Sulzer mekikçikli dokuma makinelerinde makine eninin % 50’sine kadar en azaltılması yapılarak kumaş dokunabilir.
Farklı dokuma makinesi üreticileri ve bunların farklı model dokuma makineleri, makine eninden daha düşük enlerde kumaş dokumak için farklı düzenlemelere sahiptir. Bazı firmalar sadece 200 mm en azaltılmasına izin verir. Malzeme ve kumaş tiplerindeki muhtemel değişimler göz önüne alındığında bu değer yetersiz kalmaktadır.
Düşük enlerde kumaş dokumak atkı kayıt hızlarını azaltabileceğinden tarak genişliğinin büyük kısmını kullanmak en ekonomik olanıdır. Geniş en makineler muhtemelen daha yüksek yatırım ve işletme mliyetine sahiptirler. Bazı durumlarda bir makinede yan yana belirli sayıda kumaş dokumak ekonomiktir. Geniş bir Sulzer mekikçikli dokuma makinesinde beş, altı veya yedi havlu her biri kendi içe kıvırma kenarları ile üretilebilir.
TAHAR
Çözgü ipliklerinin belirli kurallara göre, çerçevelerdeki gücü gözlerinden ve tarak dişleri arasından geçirilmesi işlemine tahar denir.
Tahar işleminin ilk aşaması olan gücü taharı, çözgü ipliklerinin çerçevelere bağlı olan gücü tellerine ait gücü gözlerinden gücü tığı ( gücü çekeceği ) yardımıyla tahar planına uygun olarak geçirilmesidir.
İkinci aşama ise tarak taharıdır. Tarak taharı çözgü ipliklerinin dokuma tarağının dişleri arasında kalan boşluklardan tarak tığı ( Tarak çekeceği ) kullanılarak tarak planına göre geçirilmesi işlemidir.
Bir örgünün en az kaç çerçeve ile dokunabileceğini ve hangi çözgünün hangi çerçevede yer alması gerektiğini gösteren işaretleme sistemine tahar planı adı verilir.
Tahar planı, dokunacak olan örgünün raporu esas alınarak çizilir. Tahar planı çiziminde temel kural örgü raporundaki aynı hareketi yapan çözgülerin belirlenmesi ve bu çözgülerin aynı çerçeveye ait olduğunun gösterilmesidir. Tahar planının desen kâğıdına çiziminde genellikle kullanılan yöntem, tahar planının örgü raporunun üzerinde yer alması ve her çerçeve için bir satır ayrılmasıdır. Çözgü ipliğini gösteren sütun ile ait olduğu çerçeveyi gösteren satırın kesiştiği noktadaki karenin içi doldurulur. Aynı işlem örgü raporundaki tüm çözgüler için tekrarlanarak tahar planı çizilir.
Tahar planı çizilirken; çerçevelerin numaralandırılması, dokuma makinesi veya numune dokuma tezgâhının çalışma şekline göre iki şekilde yapılabilir.
Örneğin; bezayağı örgüsünü oluşturan tek numaralı çözgü iplikleri aynı hareketi yani aynı bağlantıyı yaptığından aynı çerçevede toplanırlar. Benzer şekilde, çift numaralı çözgü iplikleri de grup oluşturarak ayrı bir çerçevede yer alırlar. Bezayağı örgü raporunda iki farklı çözgü hareketi bulunduğundan, bezayağı örgüsü en az iki çerçeve ile dokunur. Bu durumda herhangi bir örgünün dokunabilmesi için gereken çerçeve sayısı, örgü raporunda bulunan farklı çözgü hareketi sayısına eşittir.
Kumaşa en uzak çerçeveden başlayarak numaralandırma yapıldığında desen kâğıdında, yukarıdan aşağı doğru her satır bir çerçeveyi temsil eder. Çözgü ipliğini gösteren sütun ile ait olduğu çerçeveyi gösteren satırın kesiştiği noktadaki karenin içi doldurulur. Tahar planı çıkarılırken, aynı hareketi yapan çözgüler, çerçeve üzerine düşen yükü azaltmak amacıyla birden fazla çerçeveye dağıtılabilirler.
Bu durumda çerçeve sayısı örgü raporundaki çözgü sayısının katları olmalıdır. Örneğin, bezayağı örgüsü 2 çerçeve yerine 4, 6, 8... çerçeve ile dokunabilir. Ancak farklı bağlantı şekilleri olan çözgüler, kesinlikle aynı çerçevede toplanamazlar. Armürlü kumaşlarda desen kapasitesini arttırabilmek için farklı tahar türleri oluşturulmuştur.
Sıra tahar (düz tahar): Örgü raporundaki çözgüler sıra ile birinci çerçeveden, kullanılan son çerçeveye kadar gücülerden geçirilir. Yapılan işlem tekrar birinci çerçeveye dönülerek çözgü iplikleri bitinceye kadar tekrarlanır.
Atlamalı tahar: Bir gücüye düşen iplik adedi birden fazlaysa veya bir çerçeveye 1cm de düşen iplik adedi normalden fazla ise ipliklerin diğer çerçevelere paylaştırılması için kullanılan tahar sistemidir. Genellikle bezayağından türeyen dokularda tercih edilir.
Kumaşta iki temel hareket olduğu halde iplikler çerçeve atlanılarak geçirilerek dört veya sekiz çerçeveye dağıtılır. Çözgü ipliklerinin birbirine dolanma riskinin yüksek olduğu kalitelerde atlama işlemi yetersiz kalır. Bu durumda iplikleri birbirinden daha da uzaklaştırmak gerekir. İplikler gücülerden saten örgüsü gibi mümkün olan en uzak noktalarda geçirilirler. Bu taharlama sistemine saten tahar adı verilir.
Kırık (balıksırtı-kesik) tahar: Balık sırtı, kırık dimi gibi örgülerde, örgü raporu içinde varsayılan bir eksenin sağına veya soluna doğru belirli bir düzende aynı hareketlerin tekrarlandığı görülür. Tahar prensibine göre aynı hareketi yapan iplikler aynı çerçevede bulunması gerektiğinden şematik gösterimde tahar raporunda örgüyle uyumlu kırık yollar oluşur.
Gurup tahar: Birlikte kullanılan örgülere göre gruplar halinde ayrı ayrı düzenlenen tahar türüdür. Çok geniş raporlu örgülerde, peş peşe aynı hareketlerin farklı yönlerde tekrarlandığı örgülerde kullanılır.
Karışık tahar: Aynı hareketi tekrarlayan ipliklerin gruplamaya imkan vermediği krep gibi geniş raporlu örgülerde kullanılan tahar yöntemidir. Aynı harketi yapan ipliklerin aynı çerçevelerdeki gücülerden geçirilmesi prensibine göre düzenlenir.
Çift katlı(iki yollu) tahar: İki veya fazla çözgü levendi gerektiren kumaşlarda, çözgü yönünden takviye edilmiş kumaşlarda çözgü ipliklerinin sağım hızları farklı olduğu için sürtünmeyi azaltmak imacıyla kullanılan tahar sistemidir. İki farklı çözgünün taharları aralarında bir boşluk bırakılarak üst üste iki sıra halinde gösterilir.
El ile tahar yapma işlemi; iki işçi tarafından kontrollü şekilde yapılır. El ile yapılan tahar işleminde bütün çerçeveler tahar sehpasına asılır. Sehpanın arkasındaki tahar arkacı denilen işçi plana göre iplikleri sırasıyla tek tek sehpanın önünde duran tahar öncü denilen işçiye uzatır. Tahar öncü, gücü tığı ile tahar arkacının vermiş olduğu çözgü ipliklerini tek tek gücü gözünden geçirir. Gücü taharına birinci çerçevenin sol tarafından başlanır. Bu işlemde dikkat edilmesi gereken, tahar raporuna uygun şekilde hareket edilmesidir. İkinci işlem de gücülerden alınmış çözgü ipliklerinin dokuma tarağı dişlerinden geçirilmesidir.
Tahar yapmada kullanılan malzemeler;
1-Tahar sehpası; Tahar işleminin üzerinde yapıldığı, metal aksamdan oluşan basit çalışma ortamı sağlayan sehpalardır.
2-Çerçeveler; Dokuma makinelerinde ağızlığın açılmasında üzerinde bulunan gücülerin ve bu gücülerin gözlerinden geçirilen çözgü ipliklerinin istenilen aşağı yukarı hareketini (üretilecek kumaşın örgüsüne uygun) yapmasında kullanılan en önemli parçalardır. Dokunacak kumaşın örgü raporuna göre üzerinde bulunacak gücü sayısı değişmektedir. Çerçevelerin üzerine yüklenecek gücü sayısı çerçeve enine ve dokuma makinesinin tipine göre değişebilmektedir.
3-Gücüler; Çözgü ipliklerinin çerçevelere gruplar halinde takılı olarak bulunmasını sağlayan veya jakar sisteminde serbest olarak bulunan metal aksamlardır. Üstünde bulunan gücü gözü adı verilen delikten çözgü ipliklerinin geçirildiği metal tel ya da plakalardır. Çözgü ipliklerinin ağızlığı oluşturabilmesi için örgü hareketine göre aşağı yukarı yönlenmesi gerekmektedir. Bu hareketin çerçeveler aracılığı ile çözgüye ulaştırılmasını sağlayan ağızlığın oluşmasında önemi yüksek olan bir tahar elemanıdır.
4-Lameller; Lameller çözgü kontrol sisteminin bir parçasıdır. Lamel atma işlemi de taharcılar tarafından yapılır. Her bir çözgü teline bir adet olmak üzere tüm çözgülere lamel atılır. Lamel atma işlemi çözgüler makineye alınıp, bağlandıktan sonra yapılır. Çözgü ipliklerinin kopuşlarını kontrol etmek amacıyla mekanik veya elektrikli bir sistemle kombine çalışarak çözgü ipliği koptuğu anda dokuma makinesinin durdurulmasını sağlarlar. Lameller yapı olarak alt kısmı açık ya da kapalı olarak üretilirler. Testere adı verilen metal levhalar üzerinde görevlerini yerine getirirler. Altı açık olan tiplerin makineye takılması tahar işlemi bittikten sonra mümkündür. Kapalı tipler ise tahar işlemine başlanmadan çözgü ipliklerinin lamel gözlerinden geçirilmesi işleminden önce yapılmalıdır.
5-Dokuma Tarağı; Çözgü ipliklerinin dokunacak kumaşa düzgün ve homojen olarak dağılımını sağlayan dokuma makinesi parçasıdır. Kumaşın eninin, sıklığının ayarlanmasını sağlamaktadır. Çeşitli metal ve plastik maddelere uçlarından tutturulmuş ince metal plakalardan yapılırlar. İki metal plaka arasındaki boşluğa tarak dişi denir. Bu boşluğun 10 cm’deki adedi tarak numarası olarak ifade edilir. Tarakların sıklığa göre ayrımında tanımlanmasına yardımcı olur. Tarağın sıklığının artması üretilecek kumaşın sıklığının oranının büyük olması anlamına gelmektedir. Tarak, dokuma makinesi için değiştirilebilen sıklıklarda yapılan seyyar bir yardımcı parçasıdır. Tarak numarası seçilirken kumaşın eni, çözgü sıklığı, örgü raporu, çözgü renk raporu, çözgü ipliklerinin kalınlığı ve düğümlerinin oluşturduğu kalınlık dikkate alınarak yapılmalıdır.
6-Tarak ve Gücü Tığı; Dokuma makinesinde üretim sırasında meydana gelebilecek kopuşlarda ve tahar işlemi yapılırken dokuma hazırlıkta çözgü ipliklerinin tarak ve gücülerden geçirilmesinde kullanılan metalden imal edilmiş yardımcı tahar elemanıdır. Tarak çekeceği ve gücü çekeceği olarak adlandırılırlar. Her bir tahar ve dokuma elamanın çalışma sırasında yanında bulundurması gereken el aletidirler.
Çerçeve, Gücü, Tarak, Lamel ve Tahar Sehpasının Temizlik ve Bakımını Yapma;
Dokuma makinesinin işletme çalışma süresi içinde durma anı sadece makinenin bakıma alınması ya da herhangi bir sebeple arıza durumlarıdır. Uzun süreli çalışma sırasında makine üzerindeki parçaların sürekli ve kısa zaman içerisinde temizliğe ihtiyaç vardır. Dokuma çerçeveleri sürekli ağızlık oluşumunda aşağı yukarı hareket etmesi ve üzerinde çözgülerden dolayı almış olduğu ağırlık ile zamanla yıpranmakta veya kırılabilmektedir. Çerçevelerin sabitleme vidalarındaki gevşemeler kontrol edilmeli ve değişimi sağlanmalıdır.
Tahar işleminin yapılmadan önce gücü ve lamellerin temizliği modern temizlik makinelerinde çok basit ve hassas bir şekilde yapılabilir. Bu makinelerde gücü teli ve lamellerin geliştirilmiş fırçalar ve sirkülasyon sistemi ile tam otomatik olarak durulama ve sıcak hava ile kurutmayla temizliği yapılmaktadır.
Dokuma makinesi tarağı sürekli çözgü iplikleriyle sürtünme sırasında ham madde tipine göre çalışmayan yani ipliğin geçerken değmediği bölgelerde tıkanıklık oluşabilir. Ayrıca ortamın neminden dolayı deforme olabilir. Tarağın temizliği otomatik temizlik makineleri ile artık tezgâh üzerinde kısa bir süre içinde yapılabilmektedir. Bu makinelerde buhar ve temizleme sıvısının bileşimi ve enjektörlerin optimum konumu ile etkin temizleme en az su sarfiyatı ile gerçekleşmektedir.
Tahar işleminin yapıldığı küçük çaptaki işletmelerde ise bu temizlik işlemleri genellikle manuel olarak basınçlı hava, fırça, üstübü ve diğer yardımcı temizlik malzemeleri ile yapılabilmektedir.
El ile Lamel Dizimi
Çözgü ipliklerinin testereler adı verilen metal levhalar üzerine dizili lamellerin içinden geçirilme işlemidir. Lamellerin altı açık olanında çözgü ipliği lamelin deliğinden geçirilip testere üzerine uygun şekilde yuvasına bırakılır. Alt tarafı kapalı olan lameller ise önce testerelerden geçirilip çözgü ipliği, lameller testere üzerinde iken lamel gözünden geçirilir.
El ile Gücü Taharı Yapma
El ile gücü taharı yapılırken iki elemanın ortak çalışmasına gereksinim vardır. Görev dağılımında birinci eleman örgü raporuna göre gücü sıralamasına (çerçeveler dâhil) uyarak elindeki gücü tığını gücü gözünden geçirip ikinci elemanın vereceği çözgü ipliğini çekerek tamamladığı işlemdir. Yapılan işlem basit olmasına rağmen çok dikkat edilmesi gerekir. Yapılabilecek hataların tekrar çözümü zaman kaybına sebep olacaktır. Ayrıca telafi edilmemesi, dokunacak kumaşın görüntüsünün istenen örgü dışında bir yapıda üretilmesine yol açacaktır.
El ile Tarak Taharı Yapma
Çözgü ipliklerinin örgü raporuna göre açılan ağızlık içerisinden geçirilmesinden sonra kumaş sathına sıkıştırılmasını sağlayan tarak, tefe denilen mekanizma üzerinde yer almaktadır. Kullanılacak tarağın içerisinden geçirilecek olan çözgü ipliklerinin tek ya da daha fazla sayıda olması gerekli hesaplamalardan sonra dikkat edilmesi gereken önemli işlemlerin başında bulunmaktadır. Ayrıca tarağın toplam çözgü tel sayısının tek veya daha fazla sayıda içinden geçmesi pozisyonu düşünülerek yeterli kapasitede olması gerekmektedir.
Tarak üzerinde tarak eninde fazlalık kalacaksa bu kısım tarağın tek tarafında bırakılmaz bu boşluk hesaplanarak her iki tarafa eşit oranda bırakılır. Çözgü iplikleri için tarak üzerindeki kullanılan ene faydalı tarak eni denilmektedir. Tarak için gerekli hesap işlemlerinden sonra tarak çekeceği kullanılarak çözgü iplikleri sol ya da sağ tarafından başlanarak tarak taharı gerçekleştirilir.
Tahar makineleri olarak işletmelerde klasik kartonlu tahar makineleri de kullanılmaktadır. Bu tip tahar makineleri için dokuma makinelerinde ağızlık açma sistemlerinde kullanılan armür kartonları bulunmaktadır. Bu kartonların görevi dokunacak olan kumaşın örgüsünün taharını sonsuz karton üzerine işleyerek tahar makinesinde, taharlama işlemi yapılırken hangi çerçevenin çözgü ipliğini üzerinde bulunduracağının tespitini gerçekleştirmektir. Dokunacak olan kumaşın örgüsüne göre hazırlanacak tahar kartonunun mekanik tahar makinesinin karton yuvasına monte işlemi yapılır. Bu rapor doğrultusunda alınan hareketle iğneler yardımıyla uygun çerçeveye çözgü ipliği içinden geçirilmiş olan gücü ilave edilir. Mekanik tahar makinelerinde yapılacak tahar işleminde bilgisayar destekli bir çalışma yoktur. Genellikle işlemlerin çoğunluğu çalışan personel tarafından yürütülmektedir. Tahar makinesinin mekanik olması modern tahar makinelerine göre zaman kaybına neden olmaktadır.
Tahar Makinelerinin Ayar ve Bakımlarının Yapılması;
Tahar makinelerinde genel bakım ve ayarlar yapılarak makinenin verimli ve randımanlı bir şekilde çalışması mümkündür. Dikkat edilecek olan unsurlar periyodik olarak üretici firmanın belirlemiş olduğu sürelerde gerekli kısımların yağlanması, gereken parçaların zamanında değiştirilmesi ve zamanında bakımlarının yapılmasıdır.
Modern tahar makinelerinde genel mekanik tahar makinesi ile ayrı olarak tahar makinesinin elektronik ve bilgisayar donanıma sahip kısımlarının periyodik olarak kontrollerinin yapılması ve gerekli olan parçaların değişimi söz konusudur.
Tahar Makinesinde Taharlama Yapma;
Modern tahar makineleri lamellere, gücülere ve tarağa aynı anda tahar yapabilecek şekilde imal edilmektedirler.
Çözgü, taharlama işlemi boyunca tahar nakil arabasında kalır. Kıskaçlar yardımıyla alttan ve üstten sabitlenir. İşlem tamamlandıktan sonra tahar arabası tezgâhın içine sürülür ve tahar makinesine bağlanır.
Makine üzerinde taharlama işlemi boyunca tüm işlemlerin takip edildiği elektronik bir ekran mevcuttur. Makinede normal taharlama prensibi olarak her gücü gözünden bir çözgü teli geçirilmektedir. Ancak kenarlarda gücü gözünden farklı sayıda çözgü teli geçirilecekse işçi tarafından makineye bu talimat girilmelidir.
Çözgülerin lamel ve gücü gözlerinden geçirilmesi işlemi için esnek bir tığ kullanılır. İplikler, lameller ve gücüler teker teker tutucular tarafından alınır, işleme hazır duruma getirilir ve taharlaması yapılır. Tahar planları elektronik olarak transfer disketleri veya merkezi aktarma ağı tarafından makineye verilebilir. Bu bilgiler kontrol terminali tarafından planlanır ve muhafaza edilir. Taharlama işlemi tamamlandıktan sonra tahar makinesi sistemden ayrılır, çözgüler dokuma makinesine yerleştirilmek Tahar işlemi tamamlandıktan sonra çözgü levendi, çerçeveler, tarak ve lameller tahar arabası tarafından taşınır ve dokuma makinesine yerleştirilir. Bu sistem dokuma makinelerinin sökülmesi ve taşınması amacıyla da kullanılabilmektedir.
Tahar Makinesinin Çalışması Sırasında Dikkat Edilmesi Gerekli Şartlar
Tahar işlemi yapılırken çeşitli sebeplerden dolayı istenmeyen hatalar oluşabilmektedir. Bunlar çapraz hatası, lamel diziminde atlama hatası, gücü tahar hatası, tarak taharı hatası ve tarak izi gibi hatalardır. Bu hataların geneli el ile yapılan tahar işleminde karşımıza çıkmaktadır. Makine ile yapılan tahar işleminde bu hatalar göz önünde bulundurularak daha hassas çalışma sonucunda kaliteli ürün yapılabilmesi sağlanacaktır. Mekanik tahar makinelerinde tahar elemanının özellikle gücü ve tarak tahar işleminin yapımında sürekli gözlem yapması ve hataları anında çözmesi şarttır.
Tam otomatik tahar makinesinde yapılacak belli başlı kontroller:
- İplik algılayıcılarının kontrolü,
- Lamellerin kontrolü,
- Gücü kontrolü,
- Tahar iğnesinin kontrolü
- Dokuma tarağının kontrolü,
- Çözgü uçlarının tahar kontrolü,
- Rapor tekrarlarının kontrolü.
Yarı otomatik tahar makineleri
Dokumadaki çözgü ipliklerinin gücü, çerçeve lamellere ve de tarağa geçirilmesi için gerekli olan iki işçiden birisinin yerine bu sistemler kullanılmaktadır. Buna özel bazı transport sistemleri de eklendiğinde gerekli olan fiziksel güç büyük ölçüde hafiflemekte ve çözgülerle birlikte dokuma makinesinin diğer aksamlarıda (çerçeveler, gücü takıntıları, lameller ve taraklar) hem korunmuş olmakta hem de dokuma dairesine yüksek kaliteli bir çözgü sistemi getirilmektedir. Bu sistemin bir diğer avantajlı yönü de dokumadaki kopuş miktarının asgariye indirilmesidir.
Çözgü ipliği taharlama makineleri
Bu makine ‘’öncü’’ makine görevini yapmaktadır. Dolayısıyla taharlanacak ipliği ayırarak çözgü levendindeki tabakadan yaklaşık 10 cm kadar uzağa besleyen bir sistem durumundadır. Makine ipliğin tahar kancasıyla tutularak çekilmesine kadar bir süre bu pozisyonda kalır ve daha sonra hemen bir diğer ipliğe getirilir. Bütün bu işlem için gerekli zaman sadece 0,6 saniyedir. Makine 1,6 ile 250 tex arasında çeşitli iplikler ile çalışmaya elverişli bir yapıya sahiptir. Tahar çapraz tarağı olsa da olmasa da kullanılabilir. 1987 yılından bu yana taharlama tesislerindeki bütün makinelere ‘’temassız’’ elektronik kontrol sistemleri monte edilmektedir. Ayrıca özel bir sistemle üretilen sinyal sayesinde bir sonraki aygıtın (örneğin lamel ya da sayaç mekanizmasının) devreye girmesi güvence altına alınmıştır. Dolayısıyla çözgü ipliklerinde gevşeklik ya da başka nedenlerden dolayı meydana gelebilecek aksaklıklar techizatın çalışmasını engelleyecek nitelikte görülmemektedir. Besleme ve çalışma hızının kademesiz olarak ayarı mümkündür.
Yarı otomatik bir taharlama sisteminde bulunan parçaları:
- Çözgü verici makine ve çaprazlama tertibatı,
- Lamel besleme aparatı,
- Tahar sehpası,
- Çözgü levendi yataklama arabası,
- Tarak taharı makinesidir.
TAHAR PLANINI BULMAK İÇİN KUMAŞIN ANALİZ EDİLMESİ (DOKUMA)
Bir kumaşın analiz edilmesi; iplikleri, örgüsü, iplik sıklığı, taharı ve armür desen planı tarafından oluşturulan tüm yapıyı bulmaktır. Kumaşın analizinin yapılmasının en kolay yolu lup kullanmak veya iplik sökmektir. Bir kumaşın nasıl dokunmuş olduğu ve kullanılan dokuma tezgahı tipinin hangisi olduğunu bulmak için, kumaşın en ve boy yönünde deseninin bir raporunu bulmak önemlidir. O zaman bu açıkça işaretlenebilir ve bu işaretler içinde bulunan tüm alan analiz edilmelidir. Bu uzun süren ve sıkıcı bir işlem olabilir, çünkü bu iş için yapılacak ilk işlem kumaşta görülen bütün çözgü tellerinin hareketini özel desen kağıdına işaretlemektir. Raporun solundan sağına doğru ve üstünden altına veya altından üstüne doğru çalışılarak her atkı ipliği incelenir ve özel desen kâğıdında her çözgü ipliğinin görüldüğü yer bir kareyi doldurarak gösterilir. İplikleri uygun şekilde ayırabilmek için bir iğnenin kullanılması kolaylık sağlar. Kumaş deseni böylece belirlendikten sonra tahar ve armür desen planı bulunabilir.
Küçük kumaş örneğinde, hangisinin çözgü ipliği hangisinin atkı ipliği olduğunu anlamak zor olabilir. Eğer örnekte bir kenar var ise zorluk yoktur, ancak kenar yok ise yardımcı olacak bazı rehber faktörler vardır.
Çözgü ipliği genellikle daha güçlü olan ipliktir ve eğer kumaş pamuk veya rayon ipliklerinden oluşuyor ise pamuk ipliğinin çözgü olabileceğini varsaymak daha doğru olur. Yatay ve dikey olarak kullanılan iplik sayıları da bir rehber oluşturur ve genellikle daha fazla olanı çözgüdür.
Çözgü iplikleri genellikle daha fazla bükümlüdür ve eğer tek kat iplik ile katlı iplik birlikte kullanılmış ise katlı iplik çözgü ipliğidir. Kumaş deseninin bulunup üzerine çizildiği desen kâğıdı, taharı bulmak amacıyla başka bir desen kâğıdının altına yerleştirilir. Desenin çizilmiş olduğu desen kâğıdının sol tarafındaki birinci dikey hat birinci çözgü teli olarak kabul edilir ve tahar için kullanılacak desen kâğıdında alt sol karenin içi doldurulur ki bu da birinci çözgü telinin 1 numaralı gücü çerçevesinde geçirildiğini gösterir.
Desen kâğıdındaki ikinci dikey kareler hattı incelenir ve eğer birinci hattan değişik ise bunun anlamı bu çözgü telinin başka bir gücü çerçevesinde oluştuğudur. Bu da taharın çizildiği desen kâğıdında iki numaralı karenin doldurulması ile işaretlenir ve tüm diğer aynı dikey hatlarda bu gücü çerçevesine geçirilmiş olacaktır. Eğer üçüncü dikey hattı ilk ikiden değişik ise bu üç numaralı gücü çerçevesine geçirilmiş çözgü teli olarak üç numaralı karenin doldurulması ile gösterilir ve dördüncü dikey hatda değerleri gibi olacaktır.
Bu yöntem tüm rapor boyunca tekrarlanır, tahar desen kâğıdının her dikey hattını ele alarak tahar kâğıdındaki yeri doldurulur.
Tahar tamamlanınca armür desen planını bulmak mümkündür. Bu plan rapor boyunca olacak ve ne kadar gücü çerçevesi olacaksa o kadar dolu karesi olacaktır.
Armür desen planı kumaş deseninin yanına ilave edilir.
TAHARLAMA, ÇÖZGÜNÜN TAHARLANMASI (DOKUMA);
Çözgü ipliklerinin dokuma işleminde tek tek kontrol edilmeleri için lamel dizilmesi, istenilen şekilde ağızlık oluşturmaları için gücülerden geçirilmesi, istenilen ende kumaş oluşturmaları ve istenilen sıklıkta dokunmaları için taraktan geçirilmeleri gerekir.
Bu işlemlerin hepsine birden taharlama adı verilir.
Taharlama işleminde; çözgü iplikleri, ağızlık oluşturabilmeleri için dokuma örgüsüne göre belirlenen bir sıra ile gücülerin gözlerinden geçirilir.
Bu işleme gücü taharı denir. Çözgü ipliklerinin istenen enden ve sıklıkta dokunabilmeleri için belli bir düzen içinde tarak dişlerinden geçirilirler.
Bu işleme tarak taharı denir. Çözgü ipliklerinin dokuma sırasındaki kopuşlarını tek tek kontrol edebilmek için her ipliğe bir adet takılan lamelin dizilmesi işlemi de taharlama işlemlerinden kabul edilir.
Gücü taharının yapılışı; Temel dokuma işlemlerinden ağızlık oluşumunun gerçekleşebilmesi için çözgü ipliklerinin gücü tellerinden geçirilmesi gerekmektedir.
Çözgü ipliklerinin gücü tellerinin gözlerinden geçirilmesi dokuma örgüsünden çıkarılan tahar planına uygun olarak yapılır.
Eksantrikli ve armürlü dokumada gücü telleri çerçevelere takılıdır.Bu sistemlerde gücü taharı dokuma makinesinde veya ayrı ayrı bir yerde elle veya otomatik tahar makineleriyle yapılabilir.
Jakarlı dokuma makinelerinde ise çerçeveler olmadığı için gücü taharı işlemi dokuma makinesinde yapılır.
Armür, dokuma makinelerinde ağızlık açmak için kullanılan, bu amaçla çerçevelerin hareketini sağlayan ağızlık açma tertibatlarındandır. Dokuma makinelerinde ağızlık açma sistemlerinden armürlü ağızlık açma sistemi eksantrikli sisteme göre daha fazla çerçeveye hareket verir.
Bu sayı genel olarak 32 ile sınırlıdır, ancak özel ihtiyaçlara göre bu sayı 48 çerçeveye kadar da makinenin verimini düşürmektedir. Çerçeve adedi armür mekanizmasının yapımında belirlenir. Piyasanın ihtiyacına ve ekonomikliğe göre değişik sayılarda çalışan çerçeveli armürler üretilebilmektedir. Armürlü dokuma makinelerinde elde edilebilecek olan desen çeşidi ve motif büyüklüğü makineye takılabilen çerçeve sayısı ile sınırlıdır.
Yapıları ve çalışma prensipleri bakımından armür sitemlerini şu şekilde sınıflandırabiliriz:
>>>> Kapalı ağızlıklı armürler: Bu makinede ağızlık açıldıktan sonra atkı atılır ve atkı kumaşa sıkıştırılmak üzere tefe harekete geçmeden ağızlık kapanır. Ağızlığın kapanmasından sonra tefe tarafından atkı sıkıştırılır.
>>>> Açık ağızlıklı armürler: Bu makinelerde ağızlık açıldıktan ve atkı atıldıktan sonra atkı tefe tarafından kumaş sathına yanaştırılırken armür ağızlığı kapamaz. Atkı tam olarak kumaş sathına yanaştırıldıktan sonra kapanmadan yeni ağızlık açılır.
>>>> Üst ağızlık açan armürler: Bu makinelerde armür sadece çerçeveyi yukarı kaldırabilir.
>>>> Tam ağızlıklı armürler: Bu makinelerde hem yukarı hareket hem de aşağı hareket verilebilir. Çerçevelerin bir kısmının yukarı bir kısmının da aşağıya indirilmesiyle bu ağızlık oluşur.
>>>> Tek kurslu armürler: Çerçeve ayaklarına, platinlere hareket veren bıçak tektir. Bu bıçağın tek olması, makinede sadece üst ağızlığın açılmasını sağlar. Aynı zamanda makinenin devri de düşüktür.
>>>> Çift kurslu armürler: Bu armürlerde çerçeve ayaklarına, platinlere hareket veren bıçak çifttir. Armür de üst bıçak, alt bıçak olarak isimlendirilen iki bıçak bulunmaktadır. İki bıçağın olması hem tam ağızlığın açılmasını hem de makinenin veriminin yüksek olmasını sağlar.
Armür makineleri temel prensipleri aynı olmasına rağmen kumanda sistemlerine göre ve hareket iletimlerine göre sınıflandırılır.
>>>> Negatif hareketli armürler: Çalışma anında çerçevelerin sadece yukarı kaldırılmasını sağlayan sistemdir. Çerçevelerin geri hareketi yaylarla gerçekleştirilir. Basit yapısı sebebiyle kullanım alanı geniş bir sistemdir.
>>>> Pozitif hareketli armürler: Dokuma çerçevelerinin hem yukarı hareketini hem de geri hareketini gerçekleştirir. Genellikle ağır kumaşların dokunmasında kullanılan armür sistemidir.
Armür makineleri; hareketini, zincir yardımıyla krank milinden veya kayışlar yardımıyla motordan alır. Krank milinden hareket alan armür makineleri daha çok kullanılır.
Her çerçeve sırımlar ve demir çubuklarla 1 nu.lı eksen etrafında hareket edebilen, 2 nu.lı armür ayaklarına bağlanmıştır. Ayakların üst tarafında bulunan kertikli kısım ağızlık yüksekliğini ayarlamaya yarar. Her çerçeve için bir armür ayağı vardır. Armür ayaklarına bağlantı parçası (3) eksenli olarak bağlanmaktadır. 4a ve 4b kısımlarına, 5a ve 5b kancaları takılmıştır. Kancalar 4a ve 4b eksenleri üzerinde aşağı yukarı hareket edebilirler. Açıklanan tertibat her çerçeve için ayrı ayrı mevcuttur. Çerçevelerin ağırlığı ve geri çekme tertibatı 4a ve 4b noktalarını daima 6a ve 6b noktalarına doğru çeker. Kancaların altında 7a ve 7b ile gösterilen iki bıçak vardır.
Bu bıçakların diğer uçları 8 merkezli levyeye bağlanmıştır. Bu levyenin bir ucuna 9 kolu bağlanmış bu kolun diğer ucu da eksantrik mili üzerinden hareket alarak tefe hareketi ile ağızlık oluşumunun uyumlu çalışmasını sağlamaktadır. Kancalar 10a ve 10b çubuklarıyla 11 platinlerine bağlanmıştır. Platinler 12 nu.lı eksende hareketlidir. Her çerçeve için iki çubuk ve iki platin vardır.
Desenlendirme çıtaları (14), tomruğunun (15) üzerindedir. Tomruk makinenin her devrinde belirli bir miktar dönerek bir sonraki ağızlık için çıtaların hareketini sağlar. Armür çıtaları üzerindeki deliklere armür çivileri takılır. Bu çakılan çiviler platinleri yukarı kaldırır. Şekilde alt bıçağın sağa doğru gitmiş olduğu ve kendisine takılmış olan alt kancayı da sağa doğru çektiği görülmektedir. 4b noktası 13b sabitinden uzaklaşmış, 3 nu.lı bağlantı parçası armür ayaklarını sağa doğru çekerek çerçevelerin yukarı kalkmasını sağlamıştır.
İkinci atkıda hareket sırası üst bıçaktadır. Burada iki şey olabilir. Çerçeve örgüye göre aşağıya inecek veya yukarıdaki durumunu koruyacaktır.
Eğer platinin altına isabet eden çıtada çivi yoksa (yani delik boş bırakılmışsa) platinin 12 nu.lı eksenin sağ tarafında kalan kısmı aşağıya doğru inecek eksenin diğer tarafında bulunan kısım yukarıya kalkacaktır. Böylece platinin üzerine dayanan çubuk da yukarı kalkarak kancayı bıçaktan uzaklaştıracaktır. Bu nedenle üst kanca sağa doğru gidecek olan bıçağın hareketine uymayacak ve 4a noktası sola doğru giderken çerçeve aşağıya inecektir.
Eğer platinin altındaki çubuktaki çıtada çivi bulunuyorsa platinin sağ tarafı yukarıda kalmaya devam edecek, diğer kısmı aşağıda duracaktır. Böylece çerçeve yer değiştirmeyecektir. Bu nedenle Hatersley armürü açık ağızlık prensibine göre çalışan bir armürdür.
Yukarıdaki şekilde delikli kartonla kumanda edilen armür tertibatına takılmış sonsuz karton görülmektedir. En yaygın kullanım alanına sahip olan armür tertibatıdır. Çalışma prensibi yukarıda anlatılan desen çıtalı armür tertibatının aynısıdır. Ancak burada desenler çıtalar üzerine çakılan çiviler aracılığıyla değil, karton üzerine açılan delikler aracılığıyla okunur.
Sistemde desenin okunması platinlere bağlı iğneler aracılığıyla olur. Karton üzerinde örgüye uygun olarak açılan deliklere iğneler düşerek platinleri ve buradan da sistemi harekete geçirir.
Armür Kartonunun Hazırlanması
Dokuması yapılacak örgünün veya desenin armür planı hazırlandıktan sonra bunun armür makinesine kumanda edebilecek hâle getirilmesi için mekanik kontrollü armürler de desen kartonlarına delinerek veya desen çubuklarına çivi ya da role takılarak aktarılması sağlanır.
Armür kartonları bant hâlindedir. Çeşitli ebatlarda ve çeşitli dayanıklı malzemeden yapılmış şeritler hâlinde bulunur. İstenen rapor boyu kadar kullanılır ve en son iki ucu dayanıklı bir şekilde birleştirilerek sonsuz şerit hâline getirilir. Çıkarılan armür planına göre kartonların delinmesine sağdan sola doğru başlanılır armür kartonlarının armürdeki desen tomruğunda dönüşü saat yönündedir.
Dokunacak kumaşın ana örgüsünün yanında kumaşın kenarının da düzgün olabilmesi için bir kenar örgüsü verilir. Kenar ipliklerini oluşturacak çözgü ipleri, daha gergin veya gevşek olabilir. Bu da kumaşta hatalara sebep olur. Hataları önleyebilmek için kenarın gerginliğine göre bir örgü seçilir ve kullanılır.
Örgüsü çıkarılan kumaşın dokunabilmesi için armür planı kodlanır. Kodlama üst satırdan başlayarak sağdan sola doğru okunarak yapılır. armür planında alttaki numaralar çerçeve numaralarını, üstteki numaralar da karton delme makinesinin tuş numaralarını ifade etmektedir. Bu numara değişimi birinci çerçevenin kenara, başka bir deyişle kumaşa uzak olan çerçeve kabul edilmesinden kaynaklanmaktadır. Delme makinelerinde ise kumaşa yakın olan çerçeve birinci çerçeve kabul edilerek numaralandırma yapılmıştır. Bu konuda uygulamalarda sorun yaşanmaktadır. Karton delimlerimde kenar örgüsünün her zaman, kartonun kenar kısmına delinmiş olması esas alınmalıdır.
Kodlanan örgü daktiloya benzer bir alet tarafından desen kartonuna delinir.
Birinci sıradaki sayılar beyaz tuşlara basılarak, ikinci sıradaki sayılar kırmızı tuşlara basılarak delinir. Kartonda bir sıra delindikten sonra aletin kolu aşağıya çekilerek sıradaki diğer iki atkı hareketinin delimine geçilir.
Armür makinelerine istenilen örgüye ve desene göre kumanda edilmesini sağlamak için mekanik armürlerde kullanılan desen kartonlarının veya desen zincirlerinin hazırlanmasına öncülük eden armür planının hazırlanması gerekir. Dokumada örgülerin yapılan armür planı ile dokuma makinesi üzerinde çerçevelerin hareketi tespit edilebilmektedir. Şekilde verilen dimi örgüsünün tahar ve armür planları çıkarılmıştır.
armür planına göre 1. atkı atılırken 1, 4 ve 5 numaralı çerçeveler yukarı kaldırılacaktır. 2. atkı atılırken 1, 2 ve 5 numaralı çerçeveler yukarı kaldırılacaktır. Bu 5. atkıya kadar devam edip bir rapor tamamlanmış olur. Bu raporun tekrarı dokuma işlemi boyunca devam etmektedir. Dokuması yapılacak örgünün veya desenin armür planı hazırlandıktan sonra bunun armür makinesine aktarılması gerekmektedir. Mekanik kontrollü armürlerde desen kartonlarına delinerek veya desen çubuklarına çivi ya da role takılarak aktarılması gerekir. Genellikle mekanik kontrollü armürlerde desen kartonları kullanılmaktadır.
Anahtarın ölçüsünün somun/cıvata ölçüsüyle uygun olduğundan emin olunuz.
Tornavidaları, keski veya levye yerine kullanmayınız.
Tornavidanın ölçüsü ve tipi ile vidanın ölçü ve tipinin birbirine uygun olduğundan emin olunuz.
Kontrol kalemini amacına uygun olarak kullanınız, genel amaçlı tornavida olarak kullanmayınız.
Özellikle pense-yankeski- T Allen gibi ürünleri çekiç niyetine kullanmayınız, sap ve çene kısımlarına vurmayınız.
Sert çelik telleri pense ya da ince makaslarla kesmeyiniz.
Çekici , kendi sertliğinden daha sert malzemelerde kullanmayınız ve çekicin köşe kısımları ile çalışmayınız.
Hiçbir el aletine, daha fazla kuvvet elde etmek için uzatma kol takmayınız.
Özellikle kurbağacık anahtarlarda ve boru anahtarlarında anahtarın döndürme yönüne dikkat ediniz. Bu tarz ürünlerde hareketli çeneye yük bindirilmemesi gerekmektedir.
Dişleri aşınmış boru anahtarlarını kullanmayınız.
Malzemenin çapına uygun bir boru anahtarı kullanınız.
Lokma anahtarları havalı tabanca ile kullanmayınız. Havalı tabancalar için özel üretilen lokmaları tercih ediniz.
Segman penslerinin uç kısımlarının yıpranmamasına özen gösteriniz.
El aletlerini mutlaka amacına uygun olarak kullanınız.
El aletlerine kimyasal işlemler, bileme ve kaynak işlemleri uygulamayınız. Aletlerin şeklinde değişiklik yapmayınız.
Yıpranmış ve hatalı el aletlerini kullanmayınız.
Tekerlekli tamir dolaplarını bir yerden bir yere taşırken mutlaka çekmecelerinin kapalı ve dolabın kilitli olduğundan emin olunuz.
Çalışma esnasında, tekerlekli tamir dolaplarının tüm çekmecelerinin aynı anda açık olmamasına dikkat ediniz. Aksi takdirde dolabın denge dağılımı bozulacak ve devrilmesi söz konusu olabilecektir.
El aletlerini kullandıktan sonra mutlaka temizliğini ve bakımını yaparak muhafaza ediniz.
Mutlaka çalışma şartlarınıza uygun kişisel koruma teçhizatı kullanınız.
Yine tornavidaların kullanımında dikkat edilmesi gereken bir konu da tornavidaların uygun cıvatalarda kullanılması gerektiğidir. Düz, yıldız veya pozidriv uçlu tornavida vidanın anahtar ağzına tam olarak oturmalı ve en geniş yüzeyden kavramalıdır. Aksi halde kavrama yüzeyi (temas yüzeyi) dar olacağından tornavidanın sadece uç kısmına yük biner ve deforme olur. Pozidriv vida ile yıldız vida anahtar ağızları birbirine benzemesine rağmen, pozidriv uçlu tornavida yıldız başlı vidada kullanılırsa tornavida ucu vidanın anahtar ağzına tam olarak oturmayacağından deforme olacaktır. Ve bu aletleri kullanırken saptaki asama deliğinden uzatma kol geçirilerek kuvvet uygulanması, standartlardaki dayanım değerinin çok üstüne çıkacağından tornavidanın kırılmasına, deforme olmasına yol açar.
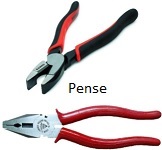
ARMÜRLERDE KULLANILAN PROGRAMLAMA MEKANİZMALARI
Program mekanizması (seçim mekanizması), program taşıyıcısından gelen sinyale bağlı olarak armürün ana milinden alınan hareketi çerçevelere iletir.
Konstrüksiyon yapısına göre program taşıyıcılar;
- Zincirli halkalı,
- Zincirli kamlı,
- Bantlı,
- Diskli,
- Elektronik
Olarak sınıflandırılmaktadır. Zincirli tekerlekli ve zincirli kamlı taşıyıcıların basit şemaları aşağıdaki şekildeki gibidir.
Bu tür program taşıyıcıları eski mekanik dokuma makinelerinde kullanılmaktadır. Program taşıyıcılar (halka ve kamlar) aynı zamanda güç iletme işlemini de üstlenmiş bulunmaktadırlar. Program zinciri uzunluğu dokunacak kumaşın örgü raporuna bağlı olarak değişmektedir.Program taşıyıcı halka ve kamların boyutları çerçevelerin yer değiştirmesi ve iletilen kuvvetin büyüklüğüne bağlı olarak değişmektedir ve bu nedenle hantal olmaktadırlar.
Bantlı ve diskli program taşıyıcıların basit işlem şemaları aşağıdaki şekilde görülmektedir.
Program okuması ve çerçevelere iletim iğneler yardımı ile gerçekleştirilmektedir. Bantlı sistemde bandın üzerinde belli hatve ile yerleşmiş program şeritleri bulunur. Şeritlerin sayısı idare edilen çerçeve sayısına eşit olmaktadır. Var yok mantığı ile çalışan bu tip mekanizmalarda var karşılığı delik, yok ise deliksiz olarak belirlenmiştir. Makinenin her türünde iğnelerin yardımı ile bantın üzerinde delik olup olmadığı kontrol edilir. İğne deliksiz alanla karşılaştığında çerçeveler alt durumdan üst duruma, deliğin içerisine daldığında ise üst durumdan alt duruma doğru yer değiştirirler.
Zincirli program taşıma mekanizmalarından farklı olarak (çerçevelere hareketin iletilmesinde mekanik güçlendiricilerin kullanılması zorunludur) bant- iğne sisteminden hareketin direkt olarak çerçevelere iletilmesi imkânsız olduğu için armürde ek mekanik güçlendiriciler kullanılmaktadır. Bu tür program taşıyıcılar içeren program mekanizmaları konstrüksiyon yapılarının karmaşık olmasına rağmen günümüzde kullanılmaktadırlar.
Elektronik program taşıyıcı olarak elektronik kasetler, disketler ve CD ler kullanılmaktadır.
İstenilen boyutta programı içerebilen ve kullanımlı olan bu tür program taşıyıcıların tek dezavantajı dokuma tezgahının ek olarak bilgisayar sistemi ile ekstradan donatılmasıdır. Eğer sistemde CD kullanılmakta ise, bir CD ye birçok desen yazılabileceği için bir desenden başka bir desene geçmek için CD değişimi söz konusu olmamaktadır. Günümüzde armür üreten firmalar elektronik armürleri ile kullanılmak üzere desen tasarım, armür kontrol ve programlama sistemlerini içeren ilave üniteler de sunmaktadırlar.
Bugün üretilen dokuma makineleri kendi bilgisayar sisteminde armür programlama ve kontrol modülüne sahip olduğundan armür üreticilerinin kontrol ünitelerine gerek duyulmaz. Ancak dokuma makineleri bilgisayar kontrollü değilse veya kendilerinin armür programlama ve kontrol ünitesi yoksa armür üreticilerinin armür programlama ve kontrol ünitelerine duyulur.
Aşağıdaki şekilde Staubli firmasına ait elektronik armür kontrol ve programlama sistemi (Staubli programming system 18) görülmektedir.
Sistem desen tasarımının yapıldığı bir bilgisayar, user software 18-58Ш/18-58IV adı verilen desen tasarım programı, taşınabilir program cihazı (portable programming device 18-58II), hafıza kartı (ram) ile veri taşıma terminali (pocket terminal 18-59II) ile armür kontrol biriminden oluşmaktadır.
Desen tasarım programı kullanılarak veya diğer bir desen tasarım sisteminde tasarlanan desen, taşınabilir programlama cihazı 18-58II’ye yüklenir. Bu cihaz 28 çerçeve için toplam 50000 atkıya kadar 1000 farklı örgü ile 9 ilave dokuma makinesi fonksiyonunun programlanmasına olanak verir. Gerekirse örgü üzerinde 18-58II cihazı kullanılarak değişiklik yapılabilir. Örgü daha sonra armür kontrol ünitesine aktarılır.
Desen verilerinin armür kontrol ünitesine yüklemenin diğer bir yolu da veri taşıma terminali 18-59II’nin kullanılmasıdır. 18-58II cihazından örgü verileri 18-59II cihazına aktarılır. Buradan da armür kontrol birimine yüklenir.
Yüklenen örgüde bir hata olduğunda düzeltme yapmak amacıyla örgü armür kontrol biriminden 18-59II cihazına ve buradan da 18-58II cihazına geri yüklenebilir. Düzeltme yapıldıktan sonra ters yol izlenerek örgü armür kontrol birimine yüklenir.
Örgüyü armür kontrol ünitesine yüklemenin yanında 18-59II cihazı ile çerçevelerin alt, orta ve üst ağızlık konumlarında seviyelenmesi, çerçevelerin sırayla hareket ettirilmesi, örgünün tersine çevrilmesi, çözgülerin 1/1 ve 2/2 örgüye göre iki tabakaya ayrılması, atılan atkı sayısının görüntülenmesi, dokuma makinesi devir sayısının görüntülenmesi, çalışan programın ID numarasının görüntülenmesi gibi ana dokuma fonksiyonlarının kontrolüne de olanak verir.
Armür kontrol üniteleri bir ağ üzerinden merkezi bir bilgisayar ile iki yönlü veri alışverişi yapılabilir. Bu yaklaşımla yukarıda bahsedilen cihazlara gerek duyulmaksızın örgülerin armür kontrol ünitelerine yüklenmesi ve gerektiğinde düzeltme yapmak için geri getirilmesi mümkündür. Ayrıca ağ üzerinden ana dokuma fonksiyonlarının kontrolü ve izlenmesi de mümkündür.
Program okuma ünitelerinin konstrüksiyon yapısını ise program taşıyıcının türü belirlemektedir. Halkalı ve kamlı program taşıyıcılı armürlerde program okunması ve uygulanmasında kullanılan konstrüksiyon aşağıdaki şekilde görülmektedir.
1 ve 2 bıçaklarına x ileri –geri yer değiştirme hareketi iletilir. 3 kancası büyük çaplı halka ile temasa geçtiğinde tahrik milinden alınan hareket kam veya kol mekanizmalarının yardımıyla 1 ve 2 numaralı bıçakların yatay eksen boyunca karşılıklı ters yönlü harekete dönüştürülür. 3 kancasının alt ve üst konumlarında olması desen zincirindeki halkaların büyük ve küçük olmasına ve hangi halka ile temasa geçildiğine bağlıdır. Büyük halka üst konumu, küçük halka alt konumu belirtmektedir. 3 kancası üst durumda olduğunda 1 bıçağı, alt durumda ise 2 bıçağı ile temasa geçerek yatay eksen boyunca sola veya sağa doğru hareket alır. Bu hareket 4 kolu vasıtası ile çerçevelere iletilir. Kancanın yukarı veya aşağı yönde hareketi 5 numaralı program halkasının çapına bağlı olmaktadır.
Makinenin her periyodunda 7 mili 360º⁄dönme açısı kadar döndürülür ve bir sonraki halka 3 kancası ile temasa girerek onun üst veya alt duruma gelmesini sağlamaktadır.
Çerçevelerin geri hareketi çözgü ipliklerine uyguladığı elastikiyet kuvvetleri yaylar tarafından gerçekleştirilir.
Bantlı ve diskli program taşıyıcılı armürlerin program okuma ünitelerinde genelde iğneli okuma sistemleri kullanılır. Programın okunması iğnenin bandın üzerinde açılmış deliğe dalması ile gerçekleştirilir. Bandın imal malzemesi karton, kâğıt veya ince plastik malzeme olabileceğinden iğnenin banda uygulayabileceği kuvvet sınırlıdır. Bu durumdan dolayı halkalı program taşıyıcı mekanizmalarından farklı olarak, iğne ile hareket iletme mekanizması arasında mekanik güçlendirici mekanizması yerleştirilir.
ÇERÇEVELERİN AYRI MOTORLAR TARAFINDAN TAHRİK EDİLDİĞİ ELEKTRONİK SİSTEMLER
Tsudakoma ve Tokyoda firmaları tarafından tekstil piyasasına sunulan diğer bir ağızlık açma mekanizması tipi ise her bir çerçevenin ayrı bir servomotor tarafından tahrik edildiği sistemlerdir.
Aşağıdaki şekilde Tsudokoma firmasına ait elektronik ağızlık açma sistemi görülmektedir. Bu sistemde her çerçeve için kullanılan motor miline sabitlenmiş diske, merkezinden belirli bir mesafede döner mafsal ile bağlanmış bir kol ve bunu izleyen kol mekanizmaları ile motorun dönme hareketi, çerçevelerin yukarı-aşağı hareketine dönüştürülür.
Makinenin ana mili ile çerçeveleri tahrik eden motorlar arasında ki zamanlama elektronik olarak gerçekleştirilir.Bu amaçla makinenin ana milinin dönüş açısını ölçen enkoderden alman pozisyon bilgisine göre motorların hareketleri kontrol edilir.
Armür ve kamlı ağızlık açma mekanizmalarından farklı olarak bu sistemde çerçevelerin hareket ve bekleme açıları (zamanları) dokunacak olan kumaş tipine bağlı olarak bilgisayardan girilip istenen değerlere ayarlanabilir.
Ayrıca ağızlık kapanma açısı da bilgisayara değer girerek elektronik olarak ayarlanabilir. Bu sistemde her çerçevenin harekete başlama ve bitiş zamanları bağımsız alarak ayarlanabildiği için aralarında zamanlama farkı meydana getirilerek aynı anda tüm çerçevelerin orta konuma gelmesi engellenebilir. Bu ayar özellikle bezayağı örgü ile yüksek çözgü sıklığına sahip kumaşların dokunması durumunda çözgü iplikleri arasındaki sürtünmeyi azaltarak çözgü kopuşlarını ve tutuşmalarını engellemek açısından önemlidir. Şekildeki sistemde motorlar aynı yönde dönmekte olup motorun yarım devrinde çerçeve bir konumdan diğerine hareket ederken motorun diğer yarım devrinde çerçeve geri hareket ederek başlangıç konumuna döner.
Motorun yarım devirlik hareketi dokuma makinesi ana milinin çerçeve hareketi için ayrılan kısmında gerçekleşir. Yani ana milinin dönüşünün 240º kısmında çerçeve hareket edip 120º kısmında bekleme yapacaksa, motorlar yarım devirlik hareketini ana mil devrinin 240º kısmında yapar. Geri kalan 120º kısmında bekler. Örgüye göre çerçevenin alt veya üst ağızlık konumlarında belirli sayıda atkı atımı esnasında bekleme yapması gerekiyorsa motorlarında bu konumda bekleme yapması gerekir.
Aşağıdaki şekil’de ise Toyoda firmasına ait ağızlık açma mekanizmasının şekli verilmektedir.
Her çerçevenin tahriki;
- Bir adet servomotor,
- Bir adet dişli mekanizması
- Eksantrik ile bunu izleyen kol mekanizmasından
Oluşmaktadır.
Servomotorlarının dönme hareketi motor mili ucundaki küçük dişliden makine gövdesine sabit olarak takılmış mil üzerine dönebilecek şekilde takılmış büyük dişliye iletilir. Bağlantı kolunun çerçeve tahrik koluna bağlantı noktası yükselterek çerçevenin daha fazla kalkış yapması sağlanır. Bu ayar temiz ağızlık oluşturmak için, arka çerçevelerin daha fazla kaldırılması için gereklidir. Çerçeve tahrik kolunun salınım hareketi kol mekanizmaları ile iki ucundan çerçeveye iletilir. Tsudakoma elektronik ağızlık açma sistemi için açıklanan özellikler bu sistem içinde geçerlidir. Her bir çerçevenin ayrı bir servomotorlar tarafından tahrik edildiği bu elektronik ağızlık açma sistemlerinde armürlerde mevcut olan yavaş çalışma ileri geri hareketin kısıtlandığı bölgeler bulunmaktadır.
Toyoda firması tarafından geliştirilen elektronik ağızlık açma sisteminde 16 çerçeveye kadar çıkılabilmektedir. Bu değer çerçevelerin ayrı motorlar tarafından tahrik edildiği armürlerde ulaşılabilen en yüksek çerçeve sayısıdır.
Dahası...
Farklı örgü raporlarına sahip kumaşların üretilmesi için değişik profillere sahip kam mekanizmaları kullanılmaktadır. Bu mekanizmaları birbirlerinden ayıran temel özellik, kamların sahip oldukları yükselme ve iniş bölgelerinin sayısıdır.
Bu temel farklılığa göre ağızlık açma sistemlerinde kullanılan kamlar;
- İki,
- Dört,
- Beş,
- Altı,
- Yedi
- Sekiz
Devirli kamlara ayrılmaktadırlar.
İki devirli kamlar sadece basit dokuma olan bezayağı dokuma için kullanılmakta ve eski dokuma tezgahlarında kullanımı yaygın olan kamlardır. Modern yüksek hızlı ve jetli dokuma tezgahlarında ise bu kamlar yerlerini kol mekanizmalarına terk etmişlerdir. Kamlı ağızlık açma sistemlerinde ise, iki devirli kamlar yerine dört devirli kamlar kullanılmaktadır.
Aşağıdaki şekil’de
dört devirli kamların profilleri, örgü elementlerinin numaraları ve grafik tasvirleri gösterilmektedir. Dört devirli kamların farklı profil sayısı üçtür. Profil sayıları az olmasına rağmen bu kamların yardımı ile kumaşların büyük bir kısmını elde etmek mümkündür.
Aşağıdaki şekil’de
beş devirli kamların profilleri, örgü elementlerinin numaraları ve grafik tasvirleri gösterilmektedir. Beş devirli kamların maksimum profil sayıları üçtür. Çeşit sayısı az olduğundan dolayı yaygın şekilde kullanılmamaktadırlar.
Aşağıdaki şekilde
altı devirli kamların profilleri, örgü elementlerinin numaraları ve grafik tasvirleri verilmektedir. Altı devirli kamların farklı profil sayısı sekizdir. Bu kamların yardımı ile çok sayıda kumaş çeşidini üretmek mümkün olmaktadır.
Aşağıdaki şekilde
yedi devirli kamların profilleri, örgü elementlerinin numaraları ve grafik tasvirleri verilmektedir. Bu kamların farklı profil sayısı dokuza eşittir. Beş devirli kamlar gibi bu kam çeşitleri de nadiren kullanılmaktadırlar.
Aşağıdaki şekilde
sekiz devirli kamların profilleri, örgü elementlerinin numaraları ve grafik tasvirleri verilmektedir. Bu kamların farklı profil sayısı yirmiye eşittir.
Raporunda atkı ve çözgü iplik sayısı sekize eşit olan yün kumaşlar, pamuk ve ipek gömleklik kumaşların büyük bir kısmı, küçük desenli elbiselik kumaşlar sekiz devirli kamlar ile üretilebilmektedir.
Farklı örgülere sahip kumaşların üretimi, örgü elemanlarına bağlı olarak kam profillerinin seçimi sonucu elde edilir. Kam profillerinin seçimi örgü raporunun solundan sağına doğru yapılmaktadır. Rapordaki ilk eleman birinci çözgüyü ifade etmektedir ve sıralama sağa doğru bu şekilde devam eder.
Aşağıdaki şekilde
altı çerçeveye sahip bir dokuma için kam profili seçimi örneği verilmektedir.
Bilindiği gibi çözgü ipliklerinin sıralı geçirilmesinde, çerçeve sayısı dokuma raporunda bulunan çözgü ipliklerinin sayısına eşittir. Bu durumda istenilen rapora sahip kumaşların üretilmesinde kullanılacak kam profili sayısı raporda yer alan çözgü ipliklerinin sayısına eşittir. Raporu oluşturan atkı ipliklerinin sayısına göre ise ana mil ile kam mili arasındaki çevrim oranı tayin edilmektedir.
Bu işlemlerden sonra kumaş desenine bağlı olarak bir sonraki kamın önceki kama göre kaydırılma açısı hesaplanmaktadır. Dört, altı ve sekiz devirli kamlar için bu açının değeri 90º, 60 º ve 45 º eşittir.
Yukarıdaki şekil incelendiğinde dokuma raporu altı çerçeveye sahiptir ve kam profili altı devirli olarak seçilmiştir. Ağızlık açma mekanizmalarında kam profili kumaş raporunda bulunan atkı ipliklerinin sayısı ile belirlenmektedir. Atkı ipliklerinin ağızlıktan geçirilmesi ana milin her bir devrinde gerçekleştiği için ağızlık açma mekanizmasının kamı örgü raporunda bulunan atkı sayısına eşit olmaktadır. Döner kamlar minimum iki bölgeden oluşurlar. Bu bölgeler yükselme ve alçalma bölgeleridir ve bu nedenle ana mil ile kam arasındaki iletim oranı minimum iki olmaktadır.
Çerçevelerin yer değiştirmesi için önemli parametreler;
- Çerçevelerin ana mile göre bekleme açısı,
- Çerçevelerin kam miline göre bekleme açısı
- Çerçevelerin ana mil ve kam miline göre yükselme ve inme açıları
Olmaktadır.
Çerçevelerin ana mile göre bekleme açısı kumaş genişliğine bağlı olarak 105º-150º arasında seçilmektedir.
Armür mekanizmaları ile ilgili yayın ve patentler incelendiğinde mekanik, elektronik ve elektromanyetik prensipler ile çalışılan armür mekanizmaları özellikle göze çarpmaktadırlar.
Patentler incelendiğinde dokuma tezgâhları için yapılan patent çalışmalarının en yoğun olarak toplandığı nokta armürlü ağızlık açma mekanizmaları olarak göze çarpmaktadır.
Bunun nedeni günümüzde yüksek hızlarda çalışma imkânı veren jetli ve rapierli dokuma makinelerinde armür mekanizmalarının yoğun olarak kullanılmasıdır.
Armür, dokuma makinelerinde ağızlık oluşturmak için kullanılan, bu amaçla çerçevelerin hareketlerini sağlayan ağızlık açma tertibatlarından birisidir. Kamlı ağızlık açma mekanizmaları, 10 adetten fazla çerçeve gerektirmeyen basit örgüye sahip kumaşların üretimi için kullanılmaktadır. Karmaşık desenli ve daha yüksek atkı raporlu kumaşların üretiminde programlanabilen armür mekanizmaları dokuma tezgahların da kullanılmaktadırlar.
Armür mekanizmaları kam mekanizmalarına göre daha komplike bir yapıya sahiptirler. Armür mekanizmalarıyla desenlendirme olanağı, eksantrikli ağızlık açma tertibatlarından fazla, jakarlı ağızlık açma tertibatından azdır. Armür mekanizmaları kumanda sistemleri itibariyle, jakar mekanizmalarının çıkış noktası sayılabilirler. Armür mekanizmaların temel olarak iki ayrı işlem söz konusudur. Bunlar; hareket iletimi ve uygun zamanda harnişler ile olan hareket iletiminin oluşturulması ve kesilmesidir.
Armür makineleri günümüzde;
- Negatif,
- Pozitif
- Rotatif
Olarak sınıflandırılmaktadır.
Fakat bu sınıflandırma altında daha geniş bir sınıflandırma yapmak mümkündür. Armür makineleri ayrıntılı olarak ağızlık açma yöntemlerine göre, strok sayılarına göre, program mekanizmalarının tipine göre, konstrüksiyon yapılarına göre ve çerçevelere hareket iletim yöntemlerine göre sınıflandırılabilir.
Ağızlık açma yöntemlerine göre armür makineleri;
- Altta kapanan ağızlık oluşturan armürler,
- Ortada kapanan ağızlık oluşturan armürler,
- Yarı açık ağızlık oluşturan armürler,
- Açık ağızlık oluşturan armürler
- Asimetrik ağızlık
Oluşturan armürler olarak sınıflandırılmaktadırlar.
Strok sayılarına göre armürler ise ikiye ayrılmaktadırlar;
- Tek stroklu
- Çift stroklu
Armürlerdir.
Bunlardan en eskileri tek stroklu armürlerdir. Bu tip armürlerde sadece bir kaldırma bıçağı ve bir dizi manivela bulunur. Her atkı atımından sonra tüm manivelalar ve çerçeveler aynı, ilk konuma dönerler. Böylece yeni kancaların bir sonraki atkı için açacağı ağızlığın çerçeveleri seçilir. Bu nedenle her atkı atılıp bittikten sonra ağızlık kapatılır ve tefeleme ağızlık kapalıyken yapılır.
Bu durumun uzun yıllardan beri yünlü dokuma sektöründe büyük avantaj sağladığı anlaşılmıştır. Atkı ipliği kapanmış ağızlıkta tefelendiği zaman, çözgülerde istenmeyen gerilim artışları olmaz ve bütün çözgü iplikleri üniform bir şekilde tek düzlemde gerilmiş olurlar. Neticede çözgü kopuşları en aza iner ve dokuma yumuşak bir biçimde yapılır.
Çift stroklu armürler ise ağızlık değiştirme kursunu, dokuma makinesinin iki devrine bölüştürerek hız limitini daha yüksek devirlere çıkarmayı başarmışlardır. Dokuma makinesinin ana milinin iki tam devrinde armür mekanizması bir tam devir yapmaktadırlar.
Programlama mekanizmalarına göre armürler ise temel olarak iki gruba ayrılmaktadır;
- Mekanik kumandalı
- Elektronik kumandalı
Armürlerdir.
Mekanik kumandalı armürlerde kendi aralarında delikli kart ile kumanda edilen ve desen zinciri vasıtasıyla kumanda edilen olmak üzere iki alt gruba ayrılmaktadırlar.
Delikli kart ile kontrol edilen armür mekanizmaları;
- Karton tipine parçalı kartonlu
- Sonsuz şerit kartonlu
Olarak ikiye ayrılırlar.
Desen zinciri ile kontrol edilen armürler ;
- Ağaç çivili
- Çelik röleli
Olmak üzere iki çeşittirler.
İlk yapılan armür mekanizmalarına ve günümüzde de birçok modern armür makinelerine mekanik olarak kumanda edilmektedir. Bu tip armürlerde programlama, kontrol elemanının tipine göre tekerlekli, küresel veya delikli karton şeklinde aparatlar yardımı ile yapılmaktadır. Modern mekanik armürlerde kartonlu kontrol elemanı daha yaygındır.
Elektronik armür makinelerinde ise programlama bilgisayar destekli üniteler vasıtası ile yapılmaktadır.
Konstrüksiyon yapılarına göre armür makineleri;
- Tek bıçaklı armür makineleri,
- Çift bıçaklı armür makineleri,
- Dişli tahrikli armür makineleri,
- Rotasyon tipli armür makineleri,
- Kol mekanizmalı armür makineleri,
- Hidrolik tahrikli armür makineleri,
- Servo motorlu armür makineleri
- Hidro-mekanik tahrikli armür makineleri
Olarak sınıflandırılmaktadırlar.
Çerçevelere hareket iletim yöntemine göre armür makineleri;
- Negatif,
- Pozitif
- Rotatif
Olmak üzere üç tipe ayrılmaktadırlar.
Negatif armürler daha basit oldukları için pozitif armürlere göre daha yaygın bir kullanım alanı bulmuşlardır ve çoğunlukla hafif, orta çözgü gerilimleri için uygundurlar. Pozitif armürler ise ağır kumaşların dokunmasında ve yüksek hızlı tezgahlarda yaygın olarak kullanılmakta, kamgarn ve ştrayhgarn dokumacılıkta tercih edilmektedirler. Orta ve yüksek çözgü gerilimi için uygun mekanizmalardır.
Kamlı ağızlık açma sistemlerine benzer şekilde, negatif armür çerçeveleri yalnızca kaldırır, indirilmesi için yaylı bir geri getirme tertibatı kullanılır. Pozitif armür ile ağızlık oluşumunda ise armür, çerçeveleri hem kaldırıp hem de indirmektedir.
Rotatif armürlerde ise dönme hareketi özel kavramaların yardımı ile çerçevelerin ileri-geri hareketine dönüştürülmektedir. Rotatif armürler yapısal olarak pozitif armür sınıfına dahil edilebilmektedirler.
İlk armür makinesinin kullanılmaya başlanmasından bugüne kadar geçen süre zarfında, çok sayıda farklı yapıya sahip armür konstrüksiyonlarının icat edildiği, bilinmektedir. Fakat bunların içerisinden çok az bir kısmı pratik olarak uygulanabilirliği mevcuttur.
Pozitif armür
Fantezi kamgarn ve ştrayhgarn kumaşlarda olduğu gibi ağır kumaşların dokumaları söz konusu olduğunda yay geri getirme tertibatına ihtiyaç göstermeyen pozitif armürlerin kullanılması uygundur. Bu sistemlerde herhangi bir geri getirme tertibatı bulunmamaktadır. Çerçevelerin tüm hareketleri mevcut armür mekanizması tarafından gerçekleştirilmektedir.
Pozitif armür sistemlerinde herhangi bir geri getirme tertibatı bulunmadığı için, kanca ile ileriye doğru çekilmiş olan salınım kolunun tekrar durdurucu traverse kadar geri getirilmesini ya da ileriye doğru çekilmesi gereken salınım kolunun bir veya iki ucunun durdurucu traverslere dayalı halde tutulmasını sağlayan bazı mekanizmalara gereksinim vardır. Öte yandan, çözgü geriliminin düşey bileşeni çerçevelerin ortada kapalı ağızlık pozisyonunda durmaları yönünde etki yapacağı için salınım kollarının kontrolsüz olarak hareket etmeleri de önlenmelidir.
Yukarıda görülen mekanizma incelendiğinde; B1 ve B2 geri çekme traversleri K1 ve K2 bıçaklarına rijit olarak bağlı haldedir ve onlarla yatay doğrultuda hareket yaparlar. Bıçaklar kendilerine takılmış olan kancaları sadece ileri doğru çekerler. Kancaların geriye doğru gelme hareketleri geri çekme traverslerinin salınım kolunun ilgili ucunu durdurucu traverslere (S1, S2) kadar itmeleriyle sağlanmaktadır. Yukarı kalkmayacak çerçevenin kancası platin vasıtasıyla yukarıda tutulur ve hizasında bulunan kanca traversine takılı halde kalır; dolayısıyla bıçak ileri giderken onunla hareket edemez. Bu sayede kancaya bağlı salınım kolu ucunun durdurucu traverse yeni desen okuma anına kadar dayalı olarak tutulması sağlanmış olmaktadır. Bu çeşit armürlerde desen okuması desen kartonları vasıtası ile yapılmaktadır.
Aşağıdaki şekilde tek stroklu ortada kapalı ağızlık oluşturan mekanik kontrollü pozitif armür örneği görülmektedir. Bu tip armürler kalın yünlü kumaşlar için kullanılmaktadırlar.
Armürde 1 numaralı çerçeveler merkezinden döner mafsalda yerleştirilmiş dikey 2 numaralı kol ile bağlanmış durumdadır. A ve B, dirsekleri olan ve kola O noktasından bağlanmış 3 numaralı bir çengel bulunmaktadır. 9 ana milinin dönme hareketi 7 krankı ve 6 kolu ile kızaklarda ileri-geri hareket yapan 4 ve 5 bıçaklara iletilir. 3 kolu üst konuma geldiğinde A kancası 4 bıçağı ile sola doğru itilir. Bu esnada 3 koluna O2 noktasından bağlanmış 2 uzvu O1 dönme ekseninde saat ibresinin tersi yönünde dönme hareketi alır. Seçim mekanizması 3 kolunun konumunu değiştirmediği sürece armür makinesinin ürettiği istemli hareket 2 uzvuna kayışla bağlanan 1 çerçeveyi, orta konum ile üst konum arasında taşır. 3 kolu alt konuma geldiği sırada B kancası 5 bıçağı ile sağa doğru çekilir ve 2 uzvu O1 dönme ekseninde saat ibresi yönünde dönme hareketi alır. Hareket programı değişmediği sürece armür mekanizmasının ürettiği ikinci istemli hareket 1 çerçevesini orta konum ile ait konum arasında taşımaktadır. 3 numaralı kolun konumunun istenen hareket programına göre hareket ettirilmesi için seçme mekanizması 10 numaralı altı yüzlü prizma ve üzerinde iki farklı çapa sahip desen baklaları bulunan 11 numaralı zincirden oluşmaktadır.
Aşağıdaki şekilde tek stroklu ortada kapalı ağızlık oluşturan elektronik kontrollü pozitif armür görülmektedir.
Yukarıdaki şekilde bu armürün üç konumdaki görünüşü verilmektedir. Ortada kapalı ağızlık prensibine göre çalışan bu armürde her atkı atımından sonra tüm çerçeveler ağızlık ortasına kadar gelir ve bir sonraki atkı için seçme işlemi yapılır.
Daha sonra desene göre çerçeveler yukarı veya aşağı hareket ederek yeni atkı için ağızlığı oluştururlar. Bundan dolayı armür mili, dokuma makinesi ile aynı hızda döner. 16 mm hatve ile 30'a kadar çerçeveyi tahrik edebilen bu armür farklı hatveler ile üretilmekte ve dokuma makinesine değişik konumlarda takılabilmektedir.
Armürün çalışma prensibi yukarıdaki şekilde görüldüğü gibi bir silindirik kam çifti ile tahrik edilen iki adet bıçak (1 ve 2 bıçağı) orta konumdan itibaren her dokuma makinesi devrinde birbirine ters yönde salinım hareketi yaparlar. 6 numaralı kolun alt ucuna döner mafsal ile bağlanmış olan 3 kancanın konumu 4 ve 5 pnömatik pistonları ile kontrol edilir. Şeklin ilk kısmında 4 pistonunun ileri konuma ve 5 pistonunun geri konuma hareket etmeleri ile 3 kancası 1 bıçağına takılır. 1 bıçağı 4 kolunu sürükleyerek birlikte Oa dönme ekseninde saat ibresi yönünde hareket ettirilir.
Bu hareket çerçevenin üst ağızlık konumuna karşılık gelir. Şeklin ikinci kısmında bıçaklar orta konumda bulunur. Bu konumda çerçevelerin hareket planına göre seçme işlemi yapılır. Çerçeve alt konuma hareket edecekse 5 pistonunun ileri ve 4 pistonunun geri konuma hareket etmeleri ile 3 kancası 2 bıçağına takılır. 2 bıçağı 4 kolunu sürükleyerek birlikte O2 dönme ekseninde saat ibresinin tersi yönünde hareket eder.
Bu konum çerçevenin alt konumuna karşılık gelir. 4 ve 5 pnömatik pistonlarının hareketi pnömo-elektro mıknatıslı valf ile elektronik olarak kontrol edilmektedir. Çerçevenin her iki yöndeki hareketi armür bıçakları tarafından sağlandığı için bu armür pozitif armür sınıfına girmektedir.
Aşağıdaki şekilde tek stroklu ortada kapalı ağızlık oluşturan elektronik kontrollü pozitif SKN armürünün kinematik şeması gösterilmiştir. Armürde çerçevelere hareket iletmek için iki adet bıçak kullanılmıştır. Çerçevenin üst konuma gelmesi 3 numaralı bıçağın 2 çengeli ile sola doğru, alt konuma gelmesi ise 8 numaralı bıçağın 9 numaralı kolun üst veya alt omuzları ile sağa doğru hareketi sırasında gerçekleşir. Çerçevelerin üst konumda beklemesi bıçakların dördünün de aynı zamanda çengelleri ile yer değiştirmesi ile elde edilir.
Çerçevelerin alt konumda beklemesi kancaların her ikisinin de 3 bıçaklarından ayrılması ile gerçekleşir. Bu esnada 2 çengelleri 6 numaralı idare edici kollar ve hareketli 4 mesnetlerinin yardımı ile 10 hareketsiz mesnetlerine dayanarak tutulurlar.
Seçim ünitesinde program taşıyıcı olarak delikli kart (11) kullanılmaktadır. 12 iğnelerinin kartı zorlamaması için üniteye 1 bıçaklarını ve onları idare ettirdikleri 13 numaralı yatay iğnelerle donatılmıştır. Eğer kartta delik açılmışa, 12 iğneleri aşağıya doğru hareket ederek 13 numaralı iğnelerini 1 bıçakları ile temasa sokar. Sola doğru yer değiştirme yapan 13 iğneleri 6 kollarını kendi eksenleri boyunca döndürerek 2 çengellerinin 3 bıçaklan ile temas etmesini sağlar.
Armürde dört ana hareket bıçağının, iki seçim bıçağının, dört sıra iğnelerin olması armürün büyük hızlarda çalışmasının engeller. Öte yandan seçim ünitesinde programı okuyabilmesi için iğnelerin kartla temasa girmesi karmaşık bir mekanik sistemle sağlanır .
Aynı işleme prensibi ile çalışan Staubli 2232 tip numaralı armürün kinematik şeması Aşağıdaki şekilde görülmektedir. Armürde 4 ve 4' numaralı bıçaklara hareket 1 ve 1' kamlarından verilir. 12 ve 12' güçlendirici bıçaklar programın okunması süresinde iğne ile kart arasında basıncın düşürülmesine yardım ederler. Bu armürün dezavantajı SKN armürleri ile aynı olmaktadır.
Bu armürün maksimum 300 dev/dak. Hızla çalışmakta ve pratik çalışma hızı 250 dev/dak dır.
Aşağıdaki şekilde tek stroklu açık ağızlık oluşturan mekanik kontrollü
- Pozitif Knowless armürü
- İngiliz Dobcross armürü
- Amerikan Crompton-Knowless armürü
Kamgarn ve ştrayhgarn dokuma makinelerinde kullanılmış ve çalışma prensibi önceki bölümlerde bahsedilen sistemlerden daha farklılık göstermektedir.
Bu armürde her bir çerçeve iki omuzlu 1 numaralı manivela ile hareket ettirilir. Manivelanın üst omzu 2 numaralı uzuv ile 4 numaralı kolun üzerinde hareketli olarak yerleştirilmiş 6 numaralı özel dişlisine bağlanmış durumdadır. 10 numaralı seçim ünitesinin 16 numaralı desen zincirinde yerleştirilen 9 numaralı program taşıyıcıları, 4 numara ile gösterilen kol ile temasa girerek 3 numaralı dişlinin 7 veya 12 numaralı sabit hızla zıt yönde dönen dişlilerle bağlantıya girmesini gerçekleştirir.
6 dişlisi 7 dişlisi ile temasa girdiğinde saat ibresinin yönünde dönme hareketi aldığından ona bağlı 2 numaralı kol sağa hareket alır ve sonuç olarak çerçeveyi üst konuma getirir. Eğer 6 dişlisi 12 dişlisi ile temasa girerse bu esnada 6 dişlisi ters yönde hareket aldığından 2 numaralı kol sola doğru hareket ederek çerçeveyi alt konuma getirecektir.
Sabit hızla dönme hareketinde bulunan dişli ile hareketsiz dişlinin ilişmeye girebilmesi ve 180° dönme hareketi aldıktan sonra temastan ayrılmasını sağlamak amacı ile 6 dişlisinin ilişmeye girme alanında bir ve karşı alnında üç dişi götürülmüştür. 7 ve 12 dişlilerininse 180°lik bir yüzeyi dişlerle kaplanmış durumdadır. Üst ve alt durumda beklemenin gerçekleştirilmesi ve dişlilerin sağlam olarak çalışması 11 -24 kamlı-kol mekanizması yardımı ile sağlanır.
NEGATİF ARMÜR
Negatif armürler daha basit oldukları için pozitif armürlere oranla daha çok kullanım alanı bulmuşlardır ve daha ziyade hafif ve orta çözgü gerilimleri için uygundurlar. Bu sistemlerin en büyük başarısı armürün bir devrinin iki atkı atımına karşılık gelmesi, dolayısıyla hareketlerin pek çoğunun yarım tezgâh hızında gerçekleştirilebilmesidir. Bu sayede daha yüksek hızlarda çalışma imkânı oluşmaktadır. Staubli firmasının ürettiği mekanik kontrollü çift stroklu açık ağızlık oluşturan bir negatif armürün şematik görünüşü aşağıda görülmektedir.
Armürün 14 numaralı tahrik mili dönme hareketini dokuma tezgahının ana milinden alır. Milin üzerindeki 15 eksantriği 16 numaralı kol ile l numaralı iki omuzlu kola bağlanmış olup üst ve alt uzuvlar 3 ve 22 numaralı mesnetlerle bağlanmış durumdadır. O1 noktasına hareketli olarak yerleştirilmiş 21 numaralı kol, O2 noktasından bağlanmış 4 numaralı balans bu nokta boyunca salınım hareketi yapabilir ve iki ucunda 4 ve 19 numaralı kancaları taşır. Balansın dönme merkezi, balans sol kenar duruma geldiğinde 1 numaralı kolun salınım merkezi ile çakışır. Bu durumda 5 veya 19 numaralı kancalardan hiçbiri 6 veya 18 numaralı idare kancaları ile bağlantıya girmemişse, 4 balansı boş hareket yapmış olur ve çerçeve alt konumda bulunur. 5 ve 19 kancalarından biri ile ilişkiye girdiği durumda ona bağlı çerçeve üst duruma gelir ve atkı atıldıktan hemen sonra geri hareket yaparak alt duruma getirilir.
Çerçevelerin alt duruma getirilmesi yayların yardımı ile gerçekleştirilir. 5 ve 19 numaralı kancaların her ikisi aynı zamanda 6 ve 8 numaralı idare edici kancalar ile bağlantıya girdiği durumda çerçevelerin üst konumda beklemesi söz konusudur.
İdare edici 6 ve 18 kancaları 9 ve l3 eksenlerinde hareketli olarak yerleşmiş iki omuzlu 8 ve 12 numaralı uzuvlara 7 ve 17 yayları ile bağlı durumdadırlar. Desen zincirine takılmış 11 baklaları 8 ve 12 numaralı iki omuzlu uzuvların programa göre idare edilmesini gerçekleştirir. 21 kolun çerçevelere hareket 23 ve 24 numaralı uzuvlardan iletilir.
Negatif armürler günümüzde mekanik ve elektronik olarak üretilmektedirler.
Aşağıdaki şekillerde Staubli firmasına ait 2521model mekanik ve 2571 model elektronik kontrollü negatif armürlerin şematik çizimleri verilmektedir.
Şekildeki Staubli firmasına ait negatif armürlerin mekanik (model 2521) ve elektronik (model 2571) program taşıyıcıları ara elemanların üzerinden A ve A’ ile gösterilen tespit kancalarını kumanda etmektedirler.
Kaldırma üniteleri, balanslar ve hareketli kancalardan oluşmaktadır. Hareket kolları tespit kancalarının hareketli bir kancayı yakalaması ile devreye girmektedirler.
Elektronik kontrollü armürde A ve A’ ile gösterilen tespit kancalarının kontrolü elektromıknatıs sayesinde yapılmaktadır. Staubli’ ye ait bu tasarımlar, azami çalışma güvenliği ile an az sayıda döner mafsal ve optimal çerçeve hareketini garanti etmektedirler.
Muratec firması negatif armür üreten diğer bir firma olup armürlerin seçme ünitesinde elektromıknatıslar yerine elektronik olarak kontrol edilen pnömatik pistonlar kullanmaktadır.
Aşağıdaki şekilde elektronik kontrollü pnömatik seçme mekanizmalı Muratec negatif armürünü gösterilmektedir.
Yukarıdaki şekilde görüldüğü gibi bir tahrik mekanizması tarafından c kolunun üst ve alt uçlarında bulunan kancaları (b ve b') tutması sağlanır. Böylece çerçevelerin yukarı konuma hareket ettirilmesi gerçekleştirilir. Pistonların ileri-geri hareket ettirilmesi elektronik olarak kontrol edilmektedir. Çerçeve alt konumdan üst konuma kaldırılacaksa önce ileri konumdaki kanca, karşısındaki kanca tarafından pistonun ileri hareketi ile tutulur. Daha sonra c kolunun salınım hareketi ile A noktası AF yarıçaplı daire yayı üzerinde saat ibresi yönünde bir miktar döner. A noktasının bu hareketi e kolu aracılığı ile f kolunun salınım hareketine dönüştürülür F kolunun salınım hareketi eğilebilir kablolarla çerçevelere iletilir. Çerçeve kalkış miktarı artırmak istenildiğinde e kolunun f koluna bağlantı noktası yukarıya kaydırılır.